Welding consumables
Welding consumables are materials consumed during the welding process, including welding rods, welding wires, welding powders, and shielding gases. These consumables play roles in connecting, filling, protecting the weld, and stabilizing the arc during welding. Choosing the right welding consumables is crucial to ensuring welding quality and efficiency.
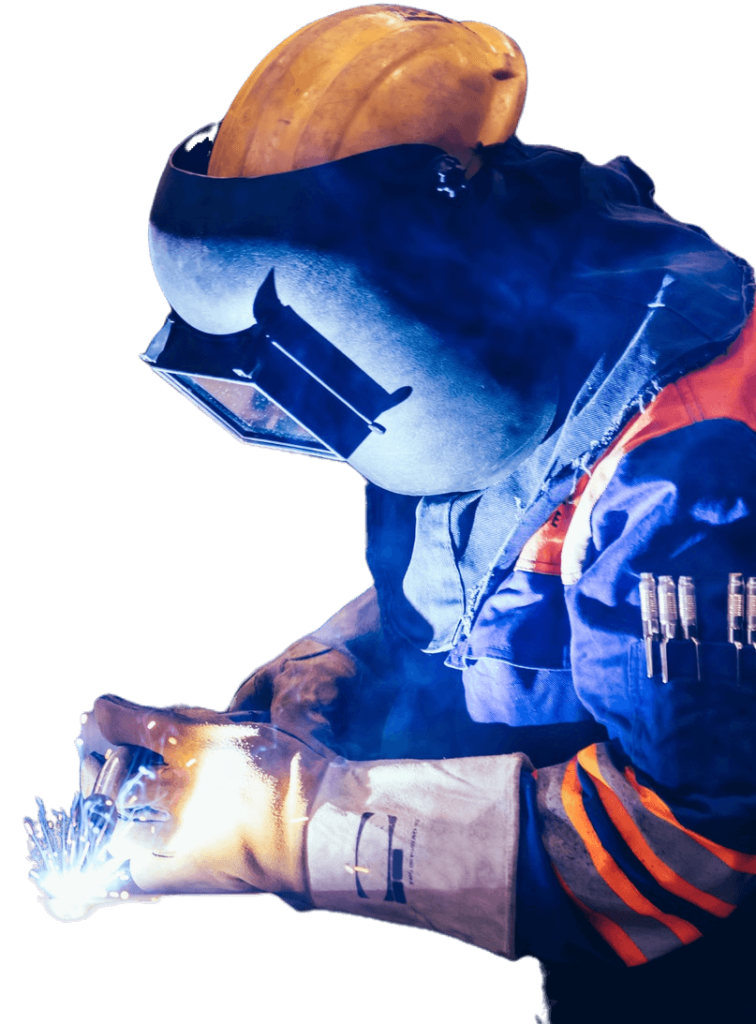
Seeking Comprehensive Welding Consumables?
WOERDE, a leading manufacturer, offers a wide array of welding consumables, including various welding wires and electrodes. Our products, adhering to international standards such as ANSI, API, DIN, GOST, BS, JIS, and China GB, cater to diverse industries globally like automotive, construction, and oil and gas.
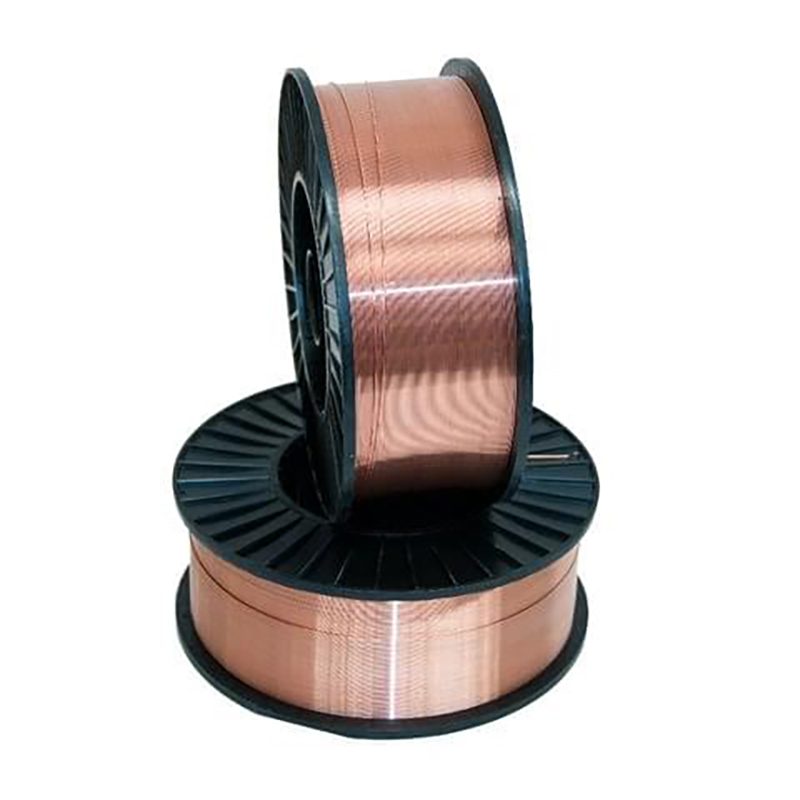
Gas-Shielded Welding Wire

Flux Cored Welding Wire
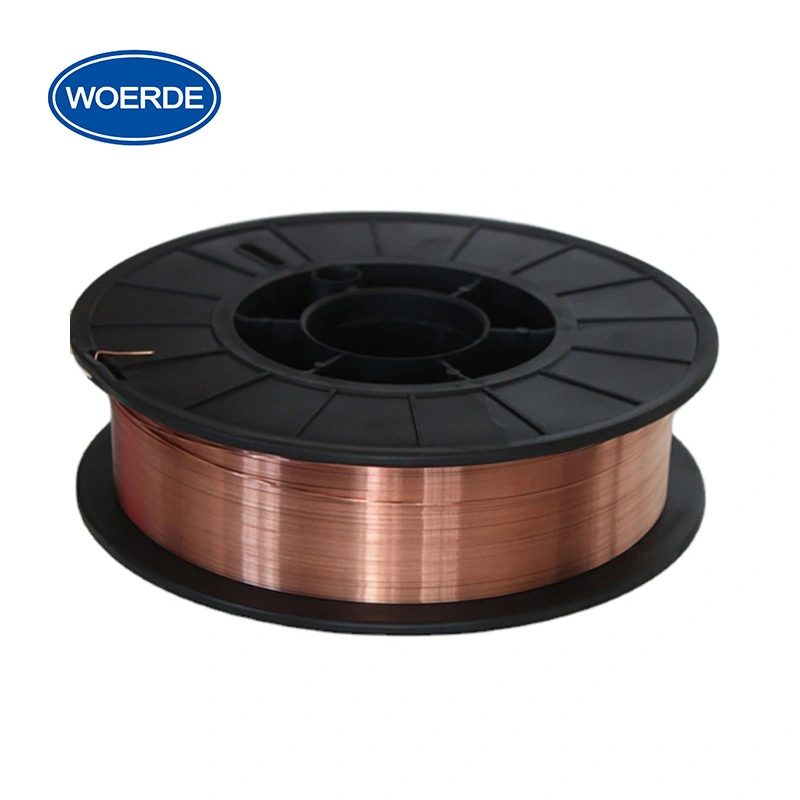
High Tensile Welding Wire
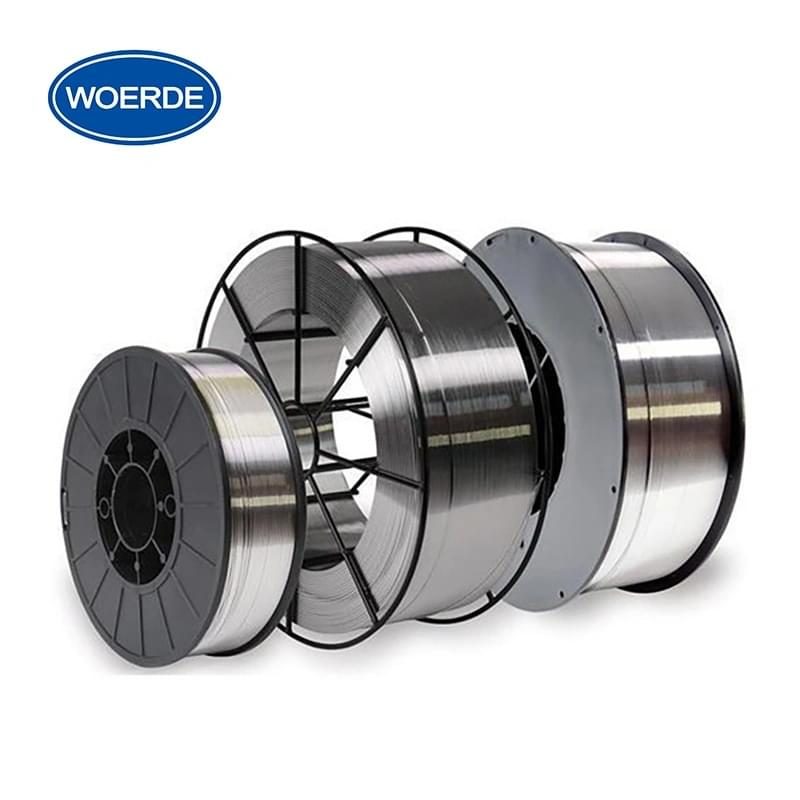
Aluminum Welding Wire
Get a free sample for testing
The Ultimate Guide to Welding Consumables
Introduction
Chapter 1
Applications of Welding Consumables
Chapter 5
Types of Welding Consumables
Chapter 2
Proper Selection of Welding Consumables
Chapter 6
Manufacturing of Welding Consumables
Chapter 3
Understanding Welding Consumables
Chapter 4
Conclusion
Chapter 8
Chapter 1
Introduction
Overview of Welding Consumables
Welding consumables are materials that are used up in the welding process and are essential to the creation of the weld. These include a variety of items such as welding rods, welding wire, flux, and shielding gas. The choice of welding consumables is crucial as it directly affects the quality of the weld, the productivity of the welding process, and the cost of welding operations.
Welding rods and wires are the materials that are melted to create the weld. They are chosen based on the type of material being welded, the welding process being used, and the desired properties of the weld. Flux is a material that prevents oxidation of the weld and base metal during the welding process. Shielding gas protects the weld pool from atmospheric contamination.
Importance of Welding Consumables in Industrial Applications
In industrial applications, welding consumables play a vital role. They are used in a wide range of industries including automotive, construction, shipbuilding, aerospace, and many more. The quality of welding consumables can significantly impact the strength and durability of the welded joints, which in turn affects the overall quality and safety of the final product.
Moreover, the choice of welding consumables can also influence the efficiency and cost-effectiveness of the welding process. For instance, using the right type of welding wire can increase welding speed and reduce the amount of post-weld cleanup, thereby saving time and reducing costs.
Introduction to WOERDE - Your Trusted Welding Consumables Supplier
WOERDE is a leading supplier of welding consumables, committed to providing high-quality products that meet the diverse needs of our customers. We understand the critical role that welding consumables play in industrial applications, and we strive to offer products that enhance the efficiency and quality of your welding processes.
Our range of products includes a wide variety of welding rods, wires, flux, and shielding gases, suitable for different types of welding processes and materials. We are dedicated to continuous innovation and improvement, ensuring that our products stay at the forefront of welding technology.
At WOERDE, we believe in building strong relationships with our customers. We offer expert advice and support to help you choose the right welding consumables for your specific needs. With WOERDE, you can trust that you are getting the best quality welding consumables, backed by excellent customer service.
Request Your Free WOERDE Welding Wire Sample
Experience WOERDE’s superior welding wires firsthand. Fill out our online form to request a free sample today. Discover why global businesses trust WOERDE.
+86-18615262155
admin@jnwoerde.com
ADD
No. 3 Road, Yuhuangmiao, Shanghe, Jinan, Shandong, China
Chapter 2
Types of Welding Consumables
Gas-Shielded Welding Wire
Gas-shielded welding wires are used in Gas Metal Arc Welding (GMAW) and Flux Cored Arc Welding (FCAW). These wires are surrounded by a shielding gas during the welding process to protect the weld pool from atmospheric contamination.
Flux-Cored Welding Wire
Flux-cored welding wire is a type of wire used in FCAW. It has a hollow core filled with flux. The flux provides the necessary shielding from the atmosphere, eliminating the need for additional shielding gas in some cases.
Solid Copper Welding Wire
Solid copper welding wire is used for welding copper and copper alloys. It provides excellent electrical conductivity and is highly resistant to corrosion.
Stainless Steel Welding Wire
Stainless steel welding wire is used for welding stainless steel materials. It provides excellent corrosion resistance and can withstand high temperatures.
Aluminum Welding Wire
Aluminum welding wire is used for welding aluminum and aluminum alloys. It has excellent thermal and electrical conductivity.
Copper Welding Wire
Copper welding wire is used for welding copper and copper alloys. It provides excellent electrical conductivity and is highly resistant to corrosion.
Welding Electrodes
Welding electrodes are used in various types of arc welding processes. They are coated with a flux that provides the necessary shielding from the atmosphere during the welding process.
Submerged Arc Wire
Submerged arc wire is used in Submerged Arc Welding (SAW). It is a process where the weld and arc zone are submerged under a blanket of granular flux, providing excellent protection from the atmosphere.
High Tensile Welding Wire
High tensile welding wire is used for welding high-strength steel. It provides excellent strength and durability to the weld.
Welding Flux
Welding flux is a material that prevents oxidation of the weld and base metal during the welding process. It also helps in maintaining the temperature of the weld pool.
Welding Machine
A welding machine is a device that provides the electric current used in the welding process. It can be used for various types of welding processes including arc welding, MIG welding, TIG welding, etc.
Welding Accessories
Welding accessories include a variety of items that support the welding process. These can include welding helmets, gloves, protective clothing, clamps, brushes, and more. They are essential for ensuring the safety and efficiency of the welding process.
Chapter 3
Manufacturing of Welding Consumables
Raw Materials and Production Process
The production of welding consumables begins with the selection of high-quality raw materials. These materials, typically various types of metals and alloys, are chosen based on their properties to meet the specific requirements of different welding applications.
The raw materials are then processed through several stages. These stages may include melting, casting, rolling, and drawing to produce welding wires and electrodes. In the case of flux-cored wires, an additional step is involved where the wire is filled with flux. The manufacturing process is carefully controlled to ensure consistency and quality in the final product.
Quality Control Measures to Ensure Reliability
Quality control is a critical aspect of the manufacturing process. At every stage of production, rigorous quality control measures are implemented to ensure the reliability and performance of the welding consumables. These measures include regular inspections and tests to monitor the quality and consistency of the products.
The quality control process also extends to the final product. Rigorous tests are conducted to ensure that the welding consumables meet the required specifications and standards. These tests may include checking the chemical composition, mechanical properties, and usability of the products.
Compliance with Industry Standards and Certifications
Compliance with industry standards and certifications is a key aspect of the manufacturing process. These standards ensure that the welding consumables meet specific quality, safety, and performance requirements.
For instance, compliance with ISO standards ensures that the products meet international quality and safety requirements. Other certifications may include those from the American Welding Society (AWS), the Canadian Welding Bureau (CWB), and the European Union (CE marking), among others. These certifications provide assurance to customers that the welding consumables are reliable and have been manufactured to the highest standards.
Chapter 4
Understanding Welding Consumables
Gas-Shielded Welding Wire - What is it and How Does it Work?
Gas-shielded welding wire is used in welding processes like Gas Metal Arc Welding (GMAW) and Flux Cored Arc Welding (FCAW). The wire is melted to form the weld, and a shielding gas is used to protect the weld pool from atmospheric contamination. The shielding gas can be inert (like argon or helium), active (like carbon dioxide), or a mixture of both, depending on the material being welded and the desired properties of the weld.
Flux-Cored Welding Wire - Advantages, Disadvantages, and Applications
Flux-cored welding wire is a type of wire that has a hollow core filled with flux. The flux provides the necessary shielding from the atmosphere, eliminating the need for additional shielding gas in some cases. This makes flux-cored welding wire advantageous for outdoor welding where wind can disperse the shielding gas. It also allows for higher welding speeds and better metal penetration. However, it can produce more smoke and spatter compared to solid wires. Flux-cored wires are commonly used in construction, shipbuilding, and other heavy fabrication industries.
Solid Copper Welding Wire - Characteristics and Typical Uses
Solid copper welding wire is used for welding copper and copper alloys. It provides excellent electrical conductivity and is highly resistant to corrosion, making it ideal for applications where these properties are important. Typical uses include welding of copper pipes in the plumbing industry, electrical connections, and in the manufacturing of copper-based products.
Stainless Steel Welding Wire - Properties and Applications
Stainless steel welding wire is used for welding stainless steel materials. It provides excellent corrosion resistance and can withstand high temperatures, making it suitable for applications in industries like food processing, chemical processing, and power generation. It is also used in the fabrication of stainless steel structures and components.
Aluminum Welding Wire - Suitable Applications and Welding Techniques
Aluminum welding wire is used for welding aluminum and aluminum alloys. It has excellent thermal and electrical conductivity, and it’s lightweight. However, welding aluminum can be challenging due to its high thermal conductivity and oxide layer. Techniques like Gas Tungsten Arc Welding (GTAW) and Gas Metal Arc Welding (GMAW) are commonly used. Applications include the aerospace industry, automotive industry, and shipbuilding.
Welding Electrodes - Types, Coatings, and Welding Positions
Welding electrodes are used in various types of arc welding processes. They are coated with a flux that provides the necessary shielding from the atmosphere during the welding process. The type of electrode is chosen based on the material being welded, the welding position, and the desired properties of the weld. The coating on the electrode can influence the stability of the arc, the ease of slag removal, and the mechanical properties of the weld. Welding electrodes can be used in all welding positions: flat, horizontal, vertical, and overhead.
Chapter 5
Applications of Welding Consumables
Industrial Applications and Industries Served
Welding consumables are used in a wide range of industrial applications. They are essential in industries such as construction, where they are used in the fabrication of steel structures; in the manufacturing sector, for the production of machinery and equipment; in the energy sector, for the construction of power plants and pipelines; and in the aerospace industry, for the manufacturing of aircraft and spacecraft. Each industry has specific requirements for welding consumables, depending on the materials used and the desired properties of the weld.
Automotive Sector and Welding Consumables
In the automotive sector, welding consumables are used in the manufacturing of various components of vehicles, including the body, chassis, and engine parts. The choice of welding consumables depends on the type of material being welded, the required strength and durability of the weld, and the production speed. High-strength steel, aluminum, and stainless steel are commonly used materials in this sector, and corresponding welding wires and electrodes are used.
Shipbuilding Industry and Welding Wire Selection
The shipbuilding industry uses welding consumables for the construction of various parts of ships, including the hull, deck, and superstructure. The choice of welding wire depends on the type of steel used, which can range from mild steel to high-strength steel. Flux-cored wires and submerged arc wires are commonly used due to their high deposition rates and excellent penetration, which increase productivity and ensure the strength and durability of the weld.
Petrochemical Equipment and Suitable Welding Consumables
In the petrochemical industry, welding consumables are used in the fabrication of equipment such as pressure vessels, heat exchangers, and pipelines. These applications often require welding consumables that can withstand high temperatures and pressures, and resist corrosion. Stainless steel welding wires and electrodes are commonly used due to their excellent corrosion resistance. For high-temperature applications, alloy-based welding consumables may be used. The selection of welding consumables in this industry is critical due to the high safety requirements and harsh operating conditions.
Chapter 6
Proper Selection of Welding Consumables
Factors to Consider When Choosing Welding Consumables
Choosing the right welding consumables is crucial for achieving a successful weld. Several factors need to be considered:
Base Metal: The type of base metal to be welded is the primary factor. The welding consumable should have similar chemical composition to the base metal to ensure compatibility and a strong weld.
Welding Process: Different welding processes require different types of consumables. For instance, MIG welding typically uses a solid wire electrode, while stick welding uses a stick electrode.
Welding Position: Some consumables are better suited for certain welding positions. For example, certain electrodes are designed specifically for overhead welding.
Mechanical Properties: The mechanical properties required in the weld, such as strength, ductility, and toughness, will influence the choice of consumable.
Cost: The cost of consumables can significantly impact the overall cost of the welding operation. It’s important to balance cost with quality and performance.
Understanding Different Welding Processes and Material Compatibility
Understanding the different welding processes and how they interact with different materials is crucial for selecting the right consumables. For instance, TIG welding is often used for thin materials and requires a tungsten electrode, while MIG welding is used for thicker materials and requires a wire electrode. Similarly, certain materials like aluminum require specific consumables (like aluminum wire) due to their unique properties.
Welding Consumables for Specific Applications and Welding Techniques
In the petrochemical industry, welding consumables are used in the fabrication of equipment such as pressure vessels, heat exchangers, and pipelines. These applications often require welding consumables that can withstand high temperatures and pressures, and resist corrosion. Stainless steel welding wires and electrodes are commonly used due to their excellent corrosion resistance. For high-temperature applications, alloy-based welding consumables may be used. The selection of welding consumables in this industry is critical due to the high safety requirements and harsh operating conditions.
Chapter 7
Welding Consumables and Industry Standards
ISO 14343-A: G 18 8 MN Compliance
ISO 14343-A: G 18 8 MN is a specific standard for stainless steel welding consumables. This standard specifies the requirements for classification of wire electrodes, wires, rods, and deposits in the as-welded condition and in the post-weld heat-treated condition for gas shielded metal arc welding of stainless and heat-resisting steels. The classification G 18 8 Mn indicates a wire electrode or rod with a nominal composition of 18% chromium, 8% nickel, and manganese.
Compliance with this standard ensures that the welding consumable is suitable for use in applications requiring high corrosion resistance, such as in the chemical and food processing industries. It also ensures that the consumable has been tested and proven to provide satisfactory performance in terms of mechanical properties and usability.
Other Recognized Industry Standards and Certifications
There are several other recognized industry standards and certifications for welding consumables, including:
AWS (American Welding Society) Standards: AWS has a series of standards for different types of welding consumables. For example, AWS A5.18 specifies the requirements for carbon steel electrodes and rods for gas shielded arc welding.
EN (European Norm) Standards: EN standards are widely recognized in Europe and many other parts of the world. For instance, EN 440 specifies the requirements for wire electrodes and deposits for gas shielded metal arc welding of non-alloy and fine-grain steels.
ASME (American Society of Mechanical Engineers) Standards: ASME provides standards for many aspects of mechanical engineering, including welding. ASME Section IX, for example, covers the qualification of welders and welding procedures.
Compliance with these standards ensures that the welding consumables meet the requirements for a specific application and that they provide reliable and consistent performance.
Welding Consumables for Specific Applications and Welding Techniques
In the petrochemical industry, welding consumables are used in the fabrication of equipment such as pressure vessels, heat exchangers, and pipelines. These applications often require welding consumables that can withstand high temperatures and pressures, and resist corrosion. Stainless steel welding wires and electrodes are commonly used due to their excellent corrosion resistance. For high-temperature applications, alloy-based welding consumables may be used. The selection of welding consumables in this industry is critical due to the high safety requirements and harsh operating conditions.
Chapter 8
Conclusion
WOERDE's Commitment to Quality and Customer Satisfaction
At WOERDE, we are deeply committed to delivering the highest quality welding consumables and services. Our dedication to quality is reflected in our rigorous manufacturing processes, stringent quality control measures, and compliance with international industry standards. We understand that our customers rely on us for their critical welding needs, and we strive to exceed their expectations in every aspect.
Choose WOERDE for Top-Quality Welding Consumables and Services
Choosing WOERDE means choosing reliability, quality, and exceptional customer service. Our wide range of welding consumables is designed to meet the diverse needs of our customers, whether they are in the automotive sector, shipbuilding industry, or any other sector that requires welding operations. With our expert advice and support, you can be confident in selecting the right welding consumables for your specific needs.
Enhance Your Welding Projects with WOERDE's Welding Solutions
In the petrochemical industry, welding consumables are used in the fabrication of equipment such as pressure vessels, heat exchangers, and pipelines. These applications often require welding consumables that can withstand high temperatures and pressures, and resist corrosion. Stainless steel welding wires and electrodes are commonly used due to their excellent corrosion resistance. For high-temperature applications, alloy-based welding consumables may be used. The selection of welding consumables in this industry is critical due to the high safety requirements and harsh operating conditions.
Request Your Free WOERDE Welding Wire Sample
Experience WOERDE’s superior welding wires firsthand. Fill out our online form to request a free sample today. Discover why global businesses trust WOERDE.
+86-18615262155
admin@jnwoerde.com
ADD
No. 3 Road, Yuhuangmiao, Shanghe, Jinan, Shandong, China