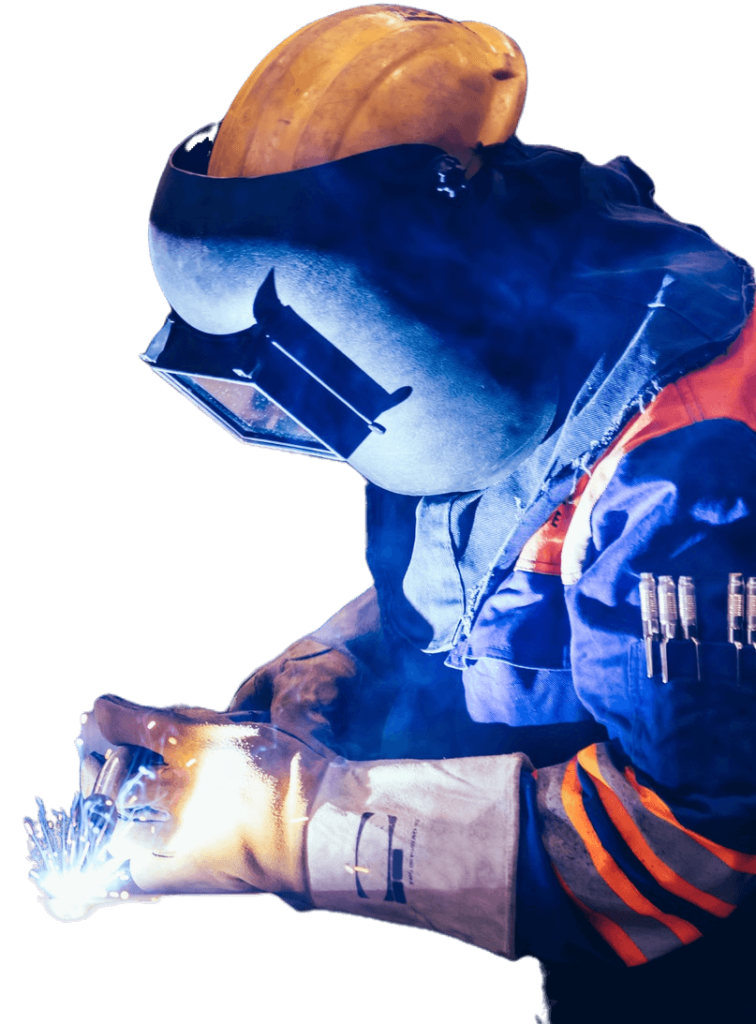
High Tensile Welding Wire
WOERDE is a leading industrial welding consumables manufacturer, offering an extensive range of High Tensile Welding Wires. Our state-of-the-art manufacturing facility in China crafts these specialized welding wires to meet the rigorous demands of various industrial applications.
Our product line includes High Tensile Welding Wires, designed for applications that require strong and resilient welds. These wires are often utilized in industries such as construction, automotive, shipbuilding, and heavy machinery manufacturing. WOERDE’s High Tensile Welding Wires are available in various AWS classifications, catering to different welding processes and material requirements.
High Tensile Welding Wire is a part of the broader family of arc welding consumables. These wires are engineered to have high tensile strength, ensuring robust and durable welds. The advantages of WOERDE’s High Tensile Welding Wire include: exceptional strength, consistent performance, and adaptability to various welding techniques. Trust in WOERDE’s quality and innovation to provide welding solutions that stand up to the most challenging industrial conditions.

AWS A5.28 ER80S-G

AWS A5.28 ER90S-G

AWS A5.28 ER110S-G

AWS A5.22 E316LT1-1
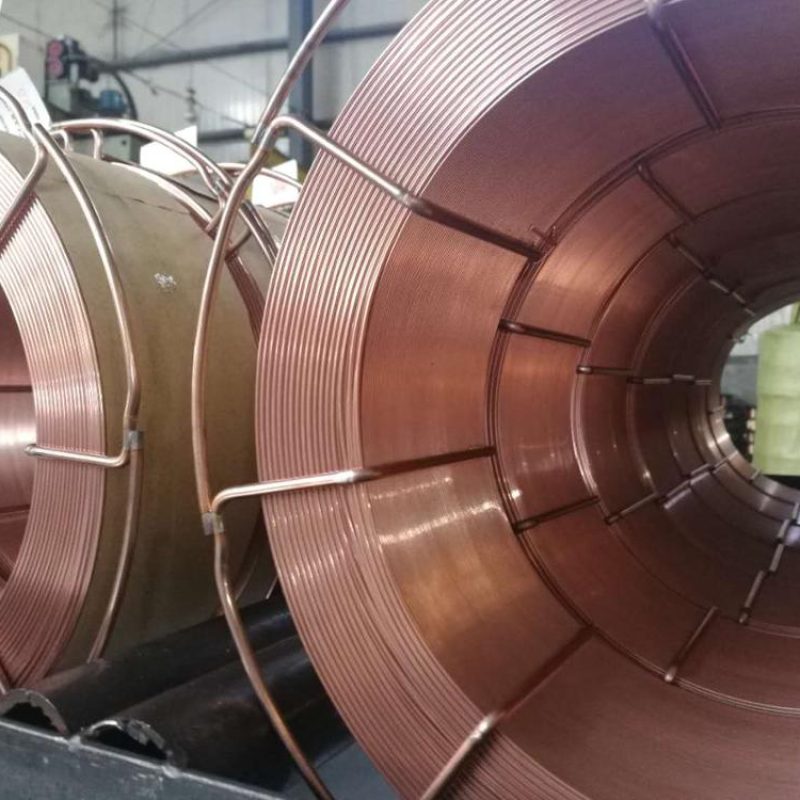
All You Need To Know About High Tensile Welding Wire
High Tensile Welding Wire is a specialized type of welding consumable designed to provide strong and resilient welds. Its high tensile strength makes it suitable for applications where durability and resistance to wear are paramount. This wire is commonly used in industries such as construction, automotive, and heavy machinery manufacturing.
Because High Tensile Welding Wire offers superior mechanical properties, it is a preferred choice for demanding industrial applications. Its high tensile strength ensures robust welds that can withstand significant stress and strain. Additionally, High Tensile Welding Wire is known for its consistent performance and adaptability to various welding techniques, including Gas Metal Arc Welding (GMAW) and Flux Cored Arc Welding (FCAW).
This article provides you with everything you need to know about High Tensile Welding Wire. What you’ll learn includes the specific uses of High Tensile Welding Wire, its composition, the technology behind its high tensile strength, and the different AWS classifications available. Towards the end, you can explore how High Tensile Welding Wire compares to other types of welding wires and understand why it’s a preferred choice for applications requiring strong and durable welds. Trust in the quality and innovation of High Tensile Welding Wire to meet the most challenging industrial welding requirements.
How Does High Tensile Welding Wire Work?
High Tensile Welding Wire is utilized as a filler material in welding processes that require enhanced strength and durability. The wire is fed through a welding gun and into the weld pool, aligning parallel to the workpiece, and an electric arc is established between the wire and the workpiece.
The diameter of High Tensile Welding Wire is carefully selected to match the specific requirements of the materials being welded, often being smaller than the thickness of those materials. As the welding operation commences, the wire melts and fuses with the base metal, forming a weld that is characterized by its high tensile strength. Depending on the process, a shielding gas may be released simultaneously from the welding gun, protecting the weld pool from atmospheric contamination. The welding process is continuous, with the wire being steadily fed and any shielding gas being consistently released, ensuring a strong and resilient weld that meets the demanding standards of various industrial applications.
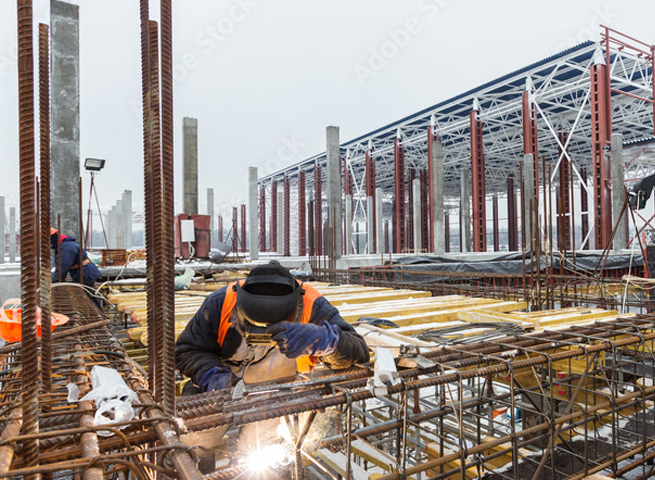
What Are High Tensile Welding Wires Used For?
High Tensile Welding Wires are designed to meet the demands of various industries that require robust welding solutions. These wires are particularly suited for applications where high strength and durability are essential. The following are some of the key industries and applications where High Tensile Welding Wires are commonly used:
- Automotive Manufacturing
- Shipbuilding Industry
- Construction Industry
- Aerospace Industry
- Pipeline Fabrication
- Heavy Equipment Manufacturing
- Railroad Construction
- Oil and Gas Industry
- Power Generation
- Metal Fabrication
Considerations When Buying Gas-Shielded Welding Wire
There are times when welding operations do not yield the desired results even if the welding wire used is of high quality. Why is this so? The answer lies in the knowledge and application of these welding wires. Understanding these considerations are part of achieving optimal welding results.
01.
Tensile Strength Requirements
- Understanding the Application: High Tensile Welding Wire is designed for applications that require superior strength and durability. Ensure that the wire’s tensile strength matches the demands of your specific project.
- Compliance with Standards: Look for wires that meet or exceed industry standards for tensile strength, ensuring that they can handle the stresses of the intended application.
02.
Compatibility with Welding Processes
- Welding Method: Determine the welding process you will be using, such as MIG or TIG, and ensure that the High Tensile Welding Wire is compatible with that method.
- Equipment Compatibility: Check that the wire can be used with your existing welding equipment, including feeders and guns.
03.
Corrosion Resistance and Environmental Considerations
- Material Composition: Consider the wire’s material composition and coatings that may enhance resistance to corrosion, especially if used in harsh or outdoor environments.
- Environmental Impact: Look for products that are manufactured with environmentally responsible practices and materials.
04.
Supplier Reputation and Support
- Quality Assurance: Choose a reputable supplier known for producing high-quality products that meet industry standards.
- Technical Support and Training: Consider suppliers that offer technical support, training, and guidance to ensure that you are using the High Tensile Welding Wire effectively and safely.
Benefits of Using High Tensile Welding Wire
Enhancing Welding Performance Across Various Applications High Tensile Welding Wire is a specialized type of welding consumable known for its high strength and versatility. Here are six key benefits that make it a preferred choice for many industrial applications
Superior Strength
- High Tensile Strength: Designed to withstand significant stress, High Tensile Welding Wire offers enhanced strength, making it suitable for heavy-duty applications.
- Durability: Its robust construction ensures that the welds remain strong and resistant to wear and tear, prolonging the life of the welded components.
Improved Weld Quality
- Consistent Welds: High Tensile Welding Wire provides consistent and uniform welds, ensuring quality and integrity in the finished product.
- Reduced Defects: Its specialized design minimizes common welding defects like cracking and porosity, leading to higher overall weld quality.
Enhanced Safety
- Reliable Performance: High Tensile Welding Wire’s reliable performance reduces the risk of weld failure, enhancing overall safety in operations.
- Compliance with Standards: Products that meet industry standards ensure that safety regulations are adhered to.
Versatility in Applications
- Wide Range of Uses: From automotive manufacturing to construction, High Tensile Welding Wire can be used in various industries that require strong and reliable welds.
- Compatibility with Different Welding Processes: It can be used with different welding methods such as MIG, TIG, and others, offering flexibility in application.
Cost-Effective
- Efficient Welding: The wire’s properties allow for efficient welding processes, reducing labor time and costs.
- Long-term Savings: Its durability means less frequent replacements and repairs, leading to long-term cost savings.
Environmentally Friendly Options
- Eco-friendly Manufacturing: Some manufacturers offer High Tensile Welding Wire produced with environmentally responsible practices.
- Recyclable Materials: Consider wires made from recyclable materials for a more sustainable choice.
Technical Specifications of High Tensile Welding Wire for MIG and TIG Welding
High Tensile Welding Wire is a vital component in both MIG (Metal Inert Gas) and TIG (Tungsten Inert Gas) welding processes. These wires are known for their high strength and are used in various industrial applications. Below is a table that outlines the key technical specifications that customers often consider when selecting High Tensile Welding Wire for MIG and TIG welding:
Specification | Description | Typical Values for MIG Welding | Typical Values for TIG Welding |
---|---|---|---|
Material Composition | The chemical composition of the wire, affecting its strength and weldability. | Carbon, Manganese, Silicon | Carbon, Manganese, Silicon |
Tensile Strength | The maximum amount of tensile stress that the wire can withstand without failure. | 70,000 – 120,000 psi | 70,000 – 110,000 psi |
Diameter | The thickness of the wire, influencing the penetration and amount of material deposited. | 0.030″ – 0.045″ | 0.030″ – 0.040″ |
Weight | The weight of the spool or coil, affecting how long the wire will last during continuous use. | 10 – 44 lbs | 10 – 36 lbs |
AWS Classification | The American Welding Society’s classification system for the wire’s mechanical properties. | E70S-6, E71T-1, etc. | ER70S-2, ER70S-6, etc. |
Welding Position | The positions in which the wire can be used (e.g., flat, horizontal, vertical, overhead). | All positions | All positions |
Shielding Gas Required | The type of shielding gas used with the wire to protect the weld pool from contamination. | CO2, Argon/CO2 mix | Argon, Argon/Helium mix |
When selecting High Tensile Welding Wire for MIG or TIG welding, it is essential to consider these specifications in conjunction with the specific requirements of your application. Consulting with a welding professional or the wire manufacturer can provide additional insights tailored to your unique needs, ensuring optimal performance and results.
Safety and Handling Instructions for High Tensile Welding Wire
High Tensile Welding Wire is known for its strength and is widely used in various industrial applications. Using this wire safely and effectively requires understanding and adherence to certain guidelines
01.
Proper Welding Technique
Utilize the correct welding technique for the specific wire type. Maintain a consistent travel speed to prevent issues such as slag inclusions. Follow the manufacturer’s guidelines for the best results.
02.
Correct Wire Diameter
Selecting the right wire diameter is crucial. Improper diameter can lead to issues like burnback and incomplete slag coverage. Consult the wire specifications for the recommended diameter for your application.
03.
Storage of Welding Wire
Store High Tensile Welding Wire in a clean, dry area to prevent exposure to moisture, which can degrade the wire quality. Proper storage ensures the wire’s integrity and performance.
04.
Temperature Considerations
Be mindful of temperature changes between the storage area and the welding environment. Sudden temperature shifts can cause condensation, leading to rusting and potential wire feeding problems.
05.
Safety Equipment
Safety is paramount. Always use appropriate safety gear, such as welding helmets, gloves, and protective clothing. Ensure proper ventilation to minimize exposure to potentially harmful fumes.
06.
Training and Certification
Proper training is essential, especially when working with specialized materials like High Tensile Welding Wire. Consider seeking additional training or certifications to master the process and ensure compliance with industry standards.
Remember, safety and adherence to best practices are vital when working with High Tensile Welding Wire. Always consult the manufacturer’s guidelines and industry standards to ensure a safe and productive work environment. By following these instructions, you can achieve optimal welding results while prioritizing safety and efficiency.
Request Your Free WOERDE Welding Wire Sample
Experience WOERDE’s superior welding wires firsthand. Fill out our online form to request a free sample today. Discover why global businesses trust WOERDE.