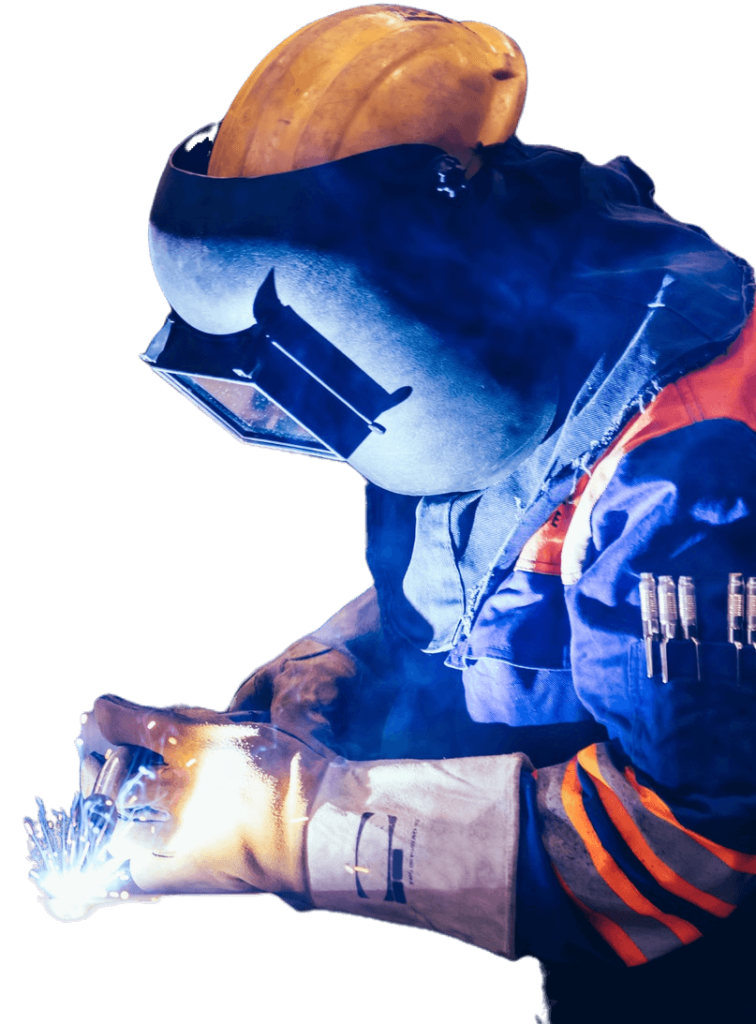
Welding Flux
WOERDE is a leading manufacturer in the industrial welding consumables sector, offering an extensive selection of welding solutions. Our state-of-the-art manufacturing facility in China is dedicated to producing top-tier WELDING FLUX, essential for high-quality welding applications.
WOERDE’s product line encompasses various types of welding consumables, including solid copper, flux-cored, stainless steel, aluminum, and copper welding wires, as well as electrodes. Our newly introduced WELDING FLUX is designed to meet the specific needs of industries such as automotive manufacturing, shipbuilding, construction, and more.
WELDING FLUX is a vital component in the family of arc welding consumables. It serves to purify and stabilize the weld pool, protecting it from atmospheric contamination and ensuring a clean, strong weld. The WELDING FLUX provided by WOERDE is formulated to deliver exceptional performance, ease of use, and reliability.
Whether you are engaged in manual or automated welding processes, WOERDE’s WELDING FLUX is engineered to enhance productivity and weld quality. Trust in WOERDE for all your welding needs, and experience the advantages of our WELDING FLUX: dependable, user-friendly, and designed for minimal maintenance.
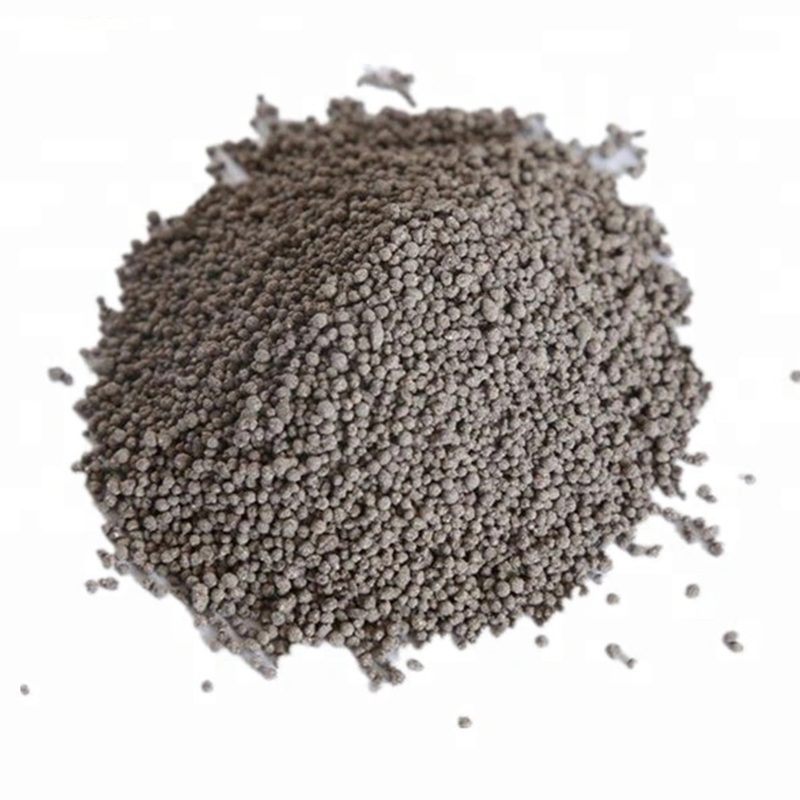
F7A4-EH14 F7A2-EM12 F7A0- EA2-A2
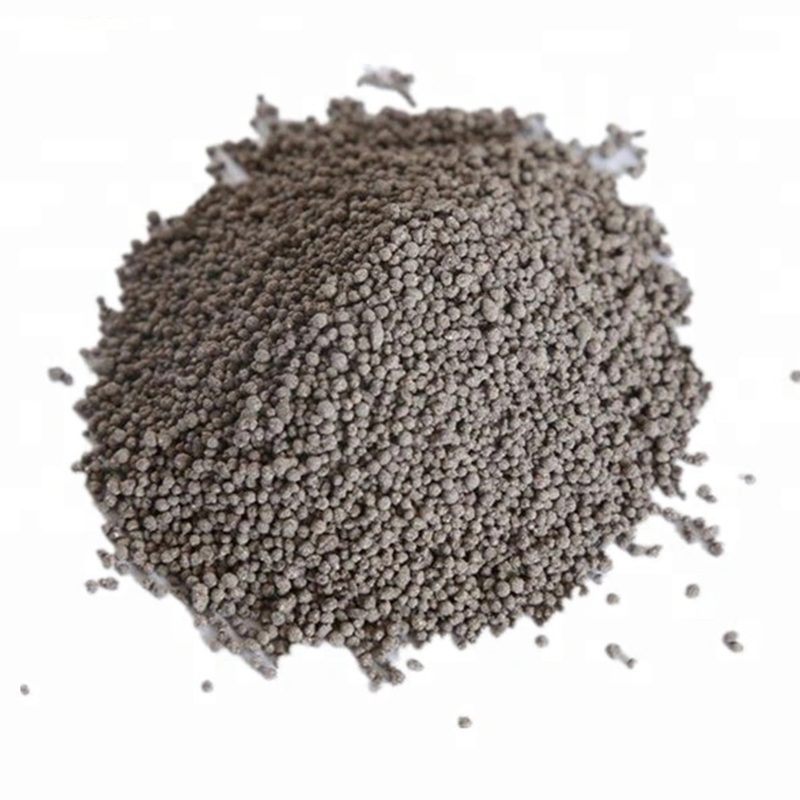
F6A2-EL12 F7A0-EM12K
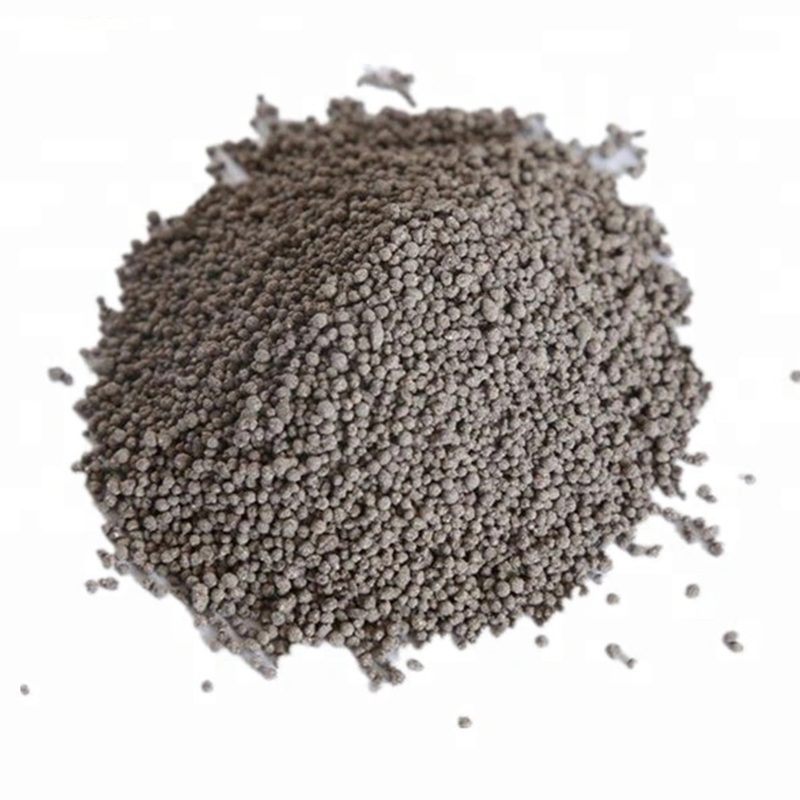
F6A2-EM12K F7A4-EH14 F7A2-EA2-A2
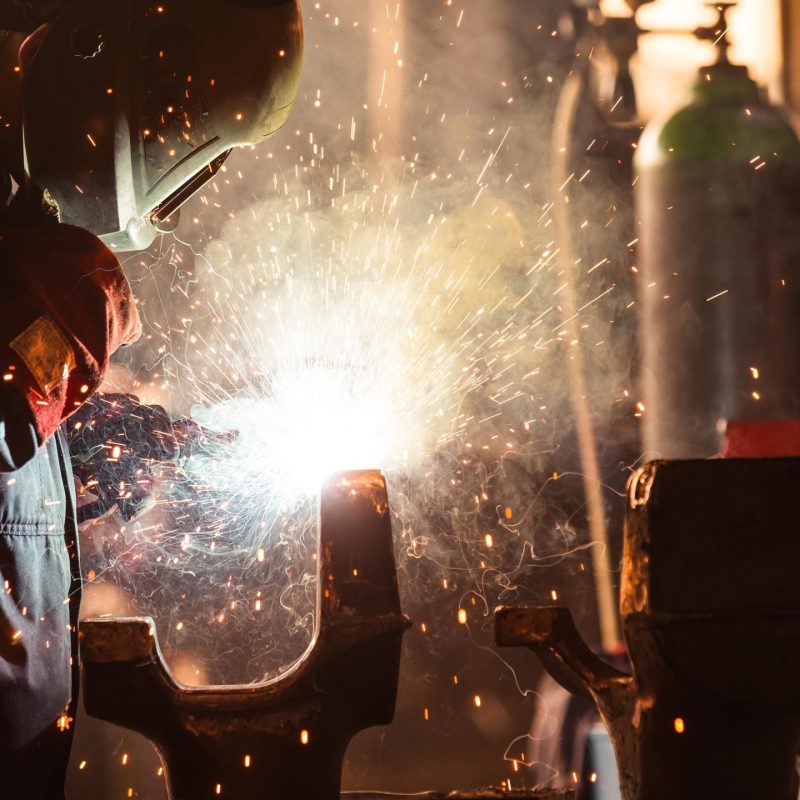
All You Need To Know About WELDING FLUX
WELDING FLUX is a crucial component in the welding process, designed to purify and stabilize the weld pool, protecting it from atmospheric contamination. Its unique formulation makes it suitable for both manual and automated welding processes, ensuring high-quality welds across various industrial applications.
Because WELDING FLUX offers exceptional performance in enhancing weld quality and is cost-effective, it is widely used in industries that require welding operations. Many industries prefer WELDING FLUX for its ease of use and minimal maintenance requirements. WELDING FLUX can be utilized in various welding processes, including Submerged Arc Welding (SAW) and Electroslag Welding (ESW).
This article provides you with everything you need to know about WELDING FLUX. What you’ll learn includes:
- Uses of WELDING FLUX:
- Composition of WELDING FLUX
- Mechanism Behind How It Works
- Different Types of WELDING FLUX
How Does WELDING FLUX Work?
WELDING FLUX primarily acts as a cleansing agent in welding operations. It is applied to the weld area where it melts, covering the molten metal and preventing oxidation and contamination from the atmosphere.
The composition of WELDING FLUX is typically tailored to match the materials being welded. When the welding operation starts, the flux melts and reacts with impurities in the base metal, floating them to the surface where they can be easily removed. This ensures a clean weld pool, free from contaminants that could weaken the weld.
Simultaneously, WELDING FLUX releases shielding gases that protect the weld pool from atmospheric contamination. This dual action of cleansing and shielding ensures a strong, clean weld, free from defects such as porosity or inclusions.
The welding process continues with the welder maintaining the appropriate temperature and travel speed, ensuring that the flux remains molten and effective throughout the weld. The solidified flux, known as slag, is then removed, revealing a high-quality weld beneath.
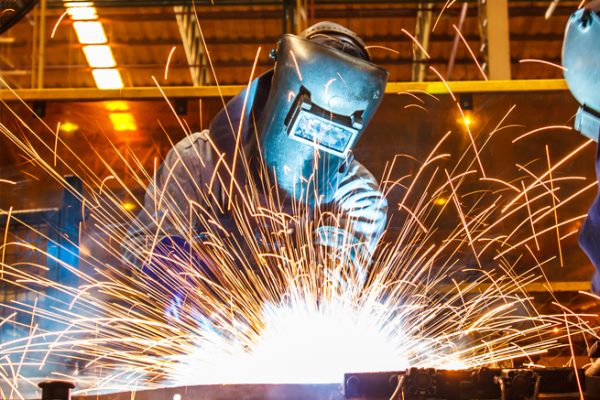
What Is Welding Flux Used For?
Welding Flux is used in a wide range of industries that require welding operations to ensure clean and strong welds. These could be the following:
- Automotive Manufacturing
- Shipbuilding Industry
- Construction Industry
- Aerospace Industry
- Pipeline Fabrication
- Heavy Equipment Manufacturing
- Railroad Construction
- Oil and Gas Industry
- Power Generation
- Metal Fabrication
Considerations When Buying Welding Flux
A Comprehensive Guide to Making the Right Choice
01.
Composition and Quality
- Composition: Understanding the chemical composition of the welding flux is vital. Different alloys require specific flux compositions to achieve optimal weld quality.
- Quality Assurance: Look for certifications or standards that ensure the flux meets industry quality requirements. High-quality flux contributes to cleaner and stronger welds.
02.
Compatibility with Welding Processes
- Process Suitability: Welding flux is used in various welding processes such as Submerged Arc Welding (SAW) and Flux-Cored Arc Welding (FCAW). Ensure that the flux is suitable for the specific welding process you intend to use.
- Material Compatibility: The flux should be compatible with the materials being welded, whether it’s steel, aluminum, or other metals.
03.
Safety and Environmental Considerations
- Handling Safety: Some fluxes may contain hazardous materials. Proper handling, storage, and disposal are essential to ensure safety.
- Environmental Impact: Consider fluxes that are environmentally friendly and comply with relevant regulations.
04.
Cost and Availability
- Budget Considerations: While quality should never be compromised, understanding the cost and choosing a flux that fits within your budget is essential.
- Supplier Reliability: Choose a reputable supplier who can provide consistent quality and timely delivery.
Benefits of Using Welding Flux
Welding Flux is a critical component in various welding processes, offering unique advantages that enhance the quality and efficiency of welding operations. Here’s an exploration of the benefits of using Welding Flux
A Cleaning Agent
Welding Flux fights against metal oxides that may attack the metal and weaken the joints. It prepares the metal to be welded, ensuring a clean and strong bond.
Protection Provider
After welding, the remaining layer of Welding Flux protects the metal from oxidizing or rusting, ensuring a weld that stays clean and robust over time.
Works on Difficult Metals
Welding Flux allows for difficult metals to be welded both to each other and a variety of other materials. It opens up possibilities for welding projects that might seem near-impossible.
Indicator for Metal Readiness
For beginners and experts alike, Welding Flux serves as an indicator that the metal is ready to make contact with the rod. It helps in timing the application of the rod perfectly.
Increases Filler Rod Flow
Using Welding Flux improves the wetting action of the filler metal, increasing the flow of the solder rod. This creates a stronger bond and eliminates problems like porosity.
Enhanced Weld Performance:
With the advancements in the welding industry, Welding Flux continues to be a viable method, offering superior weld quality and productivity. It's suitable for both manual and automated welding processes.
Technical Specifications of Gas-Shielded Welding Wire for MIG and TIG Welding
Welding Flux is an essential component in both MIG (Metal Inert Gas) and TIG (Tungsten Inert Gas) welding processes. It plays a vital role in protecting the weld pool from atmospheric contamination and enhancing the overall quality of the weld. Below are the technical specifications that customers often consider when selecting Welding Flux for MIG and TIG welding:
Feature | Specification for MIG Welding | Specification for TIG Welding |
---|---|---|
Flux Type | Agglomerated | Fused |
Grain Size | 8 to 20 mesh | 10 to 60 mesh |
Melting Point | 600°C to 850°C | 800°C to 1200°C |
Moisture Content | Less than 0.4% | Less than 0.2% |
Compatible Base Metals | Carbon Steel, Stainless Steel | Aluminum, Titanium |
Welding Position | All positions | Flat, Horizontal |
Shelf Life | 12 months | 24 months |
Packaging | 25kg bags | 50kg drums |
Understanding the Specifications:
- Flux Type: Agglomerated flux is commonly used in MIG welding, while fused flux is preferred in TIG welding.
- Grain Size: The grain size affects the flow and melting characteristics of the flux.
- Melting Point: Different melting points are suitable for various base metals and welding conditions.
- Moisture Content: Low moisture content ensures better weld quality and less spatter.
- Compatible Base Metals: Specific fluxes are designed to work with particular metals.
- Welding Position: Some fluxes are versatile and can be used in all positions, while others are position-specific.
- Shelf Life: Proper storage conditions can extend the shelf life of the flux.
- Packaging: Available in different packaging sizes to suit the needs of various projects.
Safety and Handling Instructions for Welding Flux
Using Welding Flux safely and effectively requires understanding and following certain guidelines
01.
Proper Flux Handling
Handle the flux with care to prevent contamination. Always use clean, dry tools and containers to handle the flux, as impurities can lead to weld defects.
02.
Correct Storage of Welding Flux
Store Welding Flux in a clean, dry area. Exposure to moisture or other contaminants can damage the flux, resulting in poor weld quality. Sealed containers are recommended for storage to reduce chances of problems from moisture exposure.
03.
Temperature Considerations
Maintain the same temperature in the storage area as in your welding area. Sudden temperature changes can cause condensation on the flux, leading to potential problems in the weld.
04.
Safety Equipment
Always use appropriate safety gear, including masks, gloves, and protective clothing. Welding Flux may contain substances that require proper handling and protection.
05.
Mixing and Preparation
Follow the manufacturer's guidelines for mixing and preparing the flux. Incorrect preparation can lead to inconsistencies in the weld. Ensure that the flux is well-mixed and free from lumps before use.
06.
Disposal Considerations
Dispose of used or excess flux according to local regulations and manufacturer's guidelines. Incorrect disposal can lead to environmental issues.
Remember, safety should always be your top priority when working with Welding Flux and related materials. Always follow manufacturer guidelines and industry best practices to ensure a safe and productive work environment. If you’re new to using Welding Flux, you may want to seek out additional training or certifications to help you master the process.
Request Your Free WOERDE Welding Wire Sample
Experience WOERDE’s superior welding wires firsthand. Fill out our online form to request a free sample today. Discover why global businesses trust WOERDE.