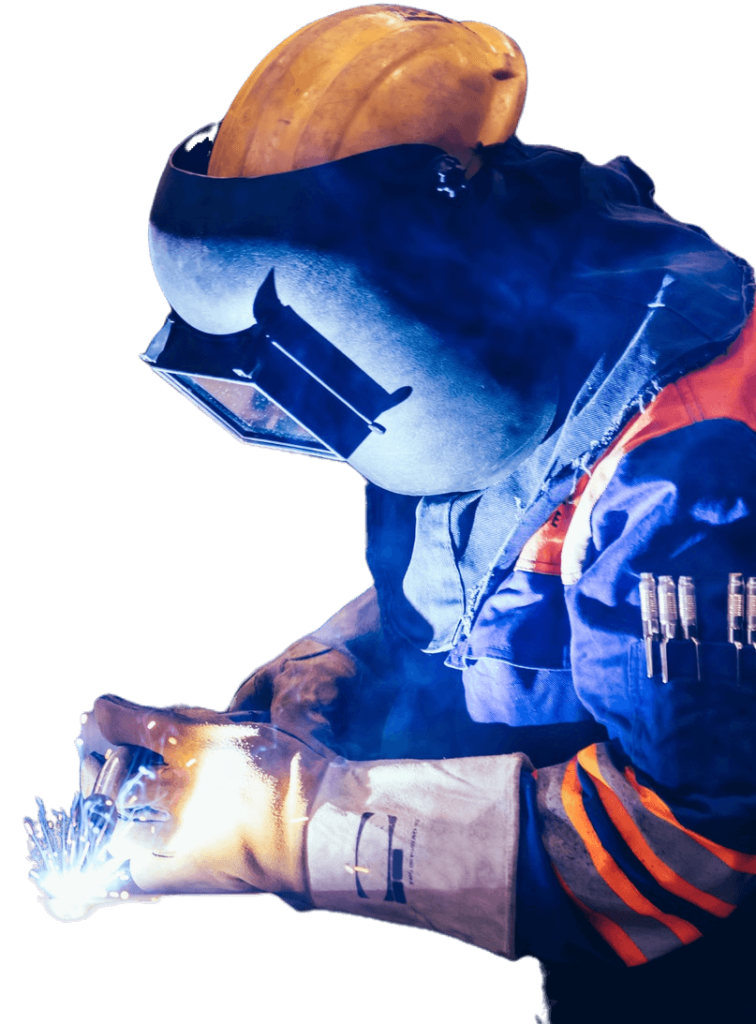
Flux Cored Welding Wire
WOERDE, a renowned industrial welding consumables manufacturer, produces high-quality Flux Cored Welding Wire in our advanced facility in China. This specialized wire is part of our diverse product range, including solid copper, stainless steel, aluminum, and other welding wires.
Flux Cored Welding Wire is designed for various industrial applications such as construction and heavy machinery manufacturing. Unlike traditional wires, it contains a flux core, providing shielding gas to protect the weld pool. WOERDE’s Flux Cored Welding Wire offers benefits like increased deposition rates, improved weld appearance, and reduced maintenance, making it a reliable and efficient choice for professionals.
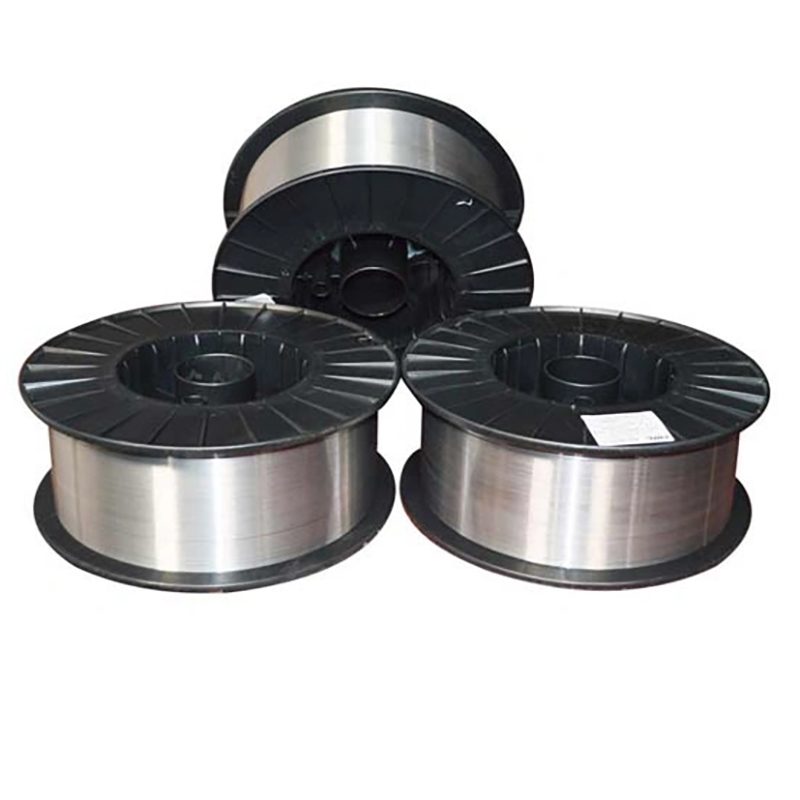
E71T-1C/9C
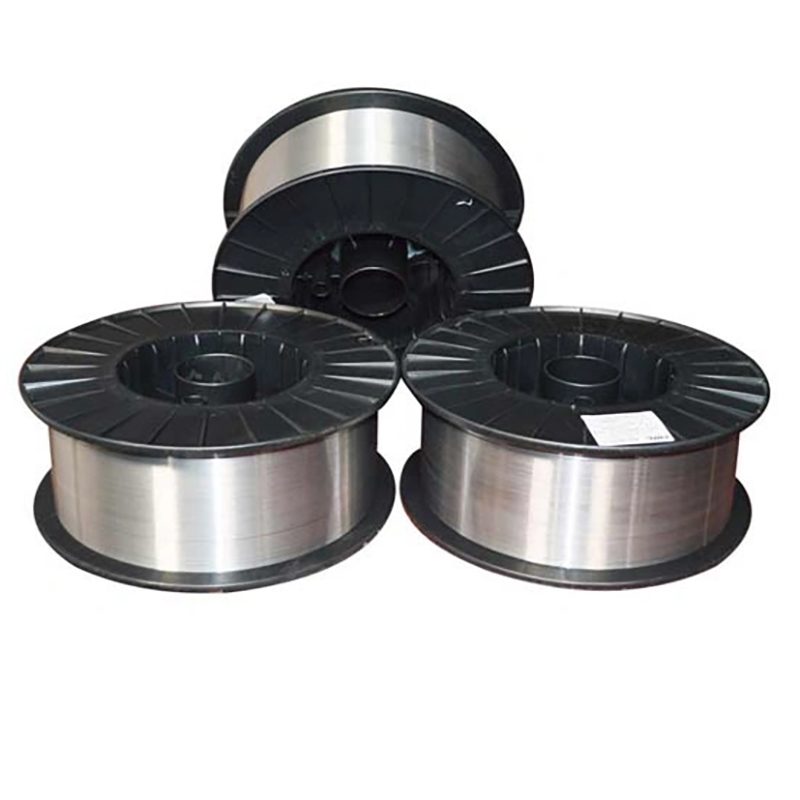
E71T-1C-J
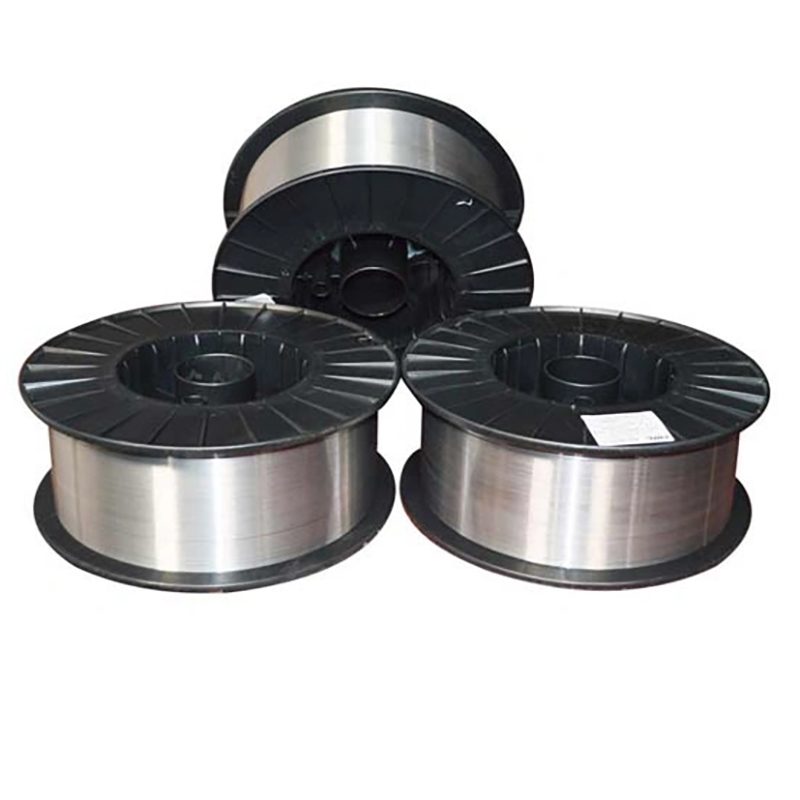
E70T-1C
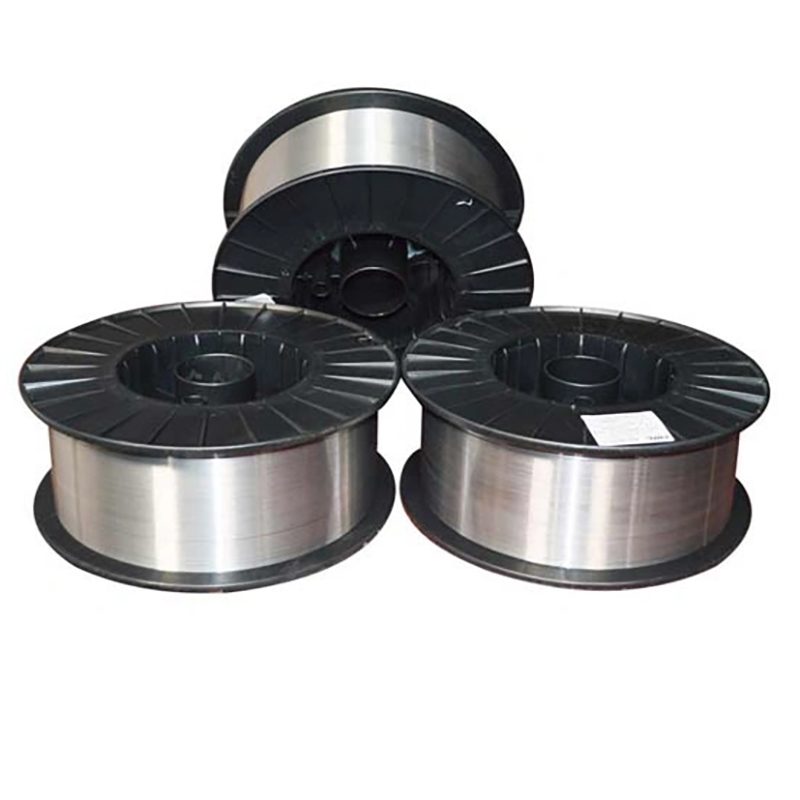
E71T-5C/5M
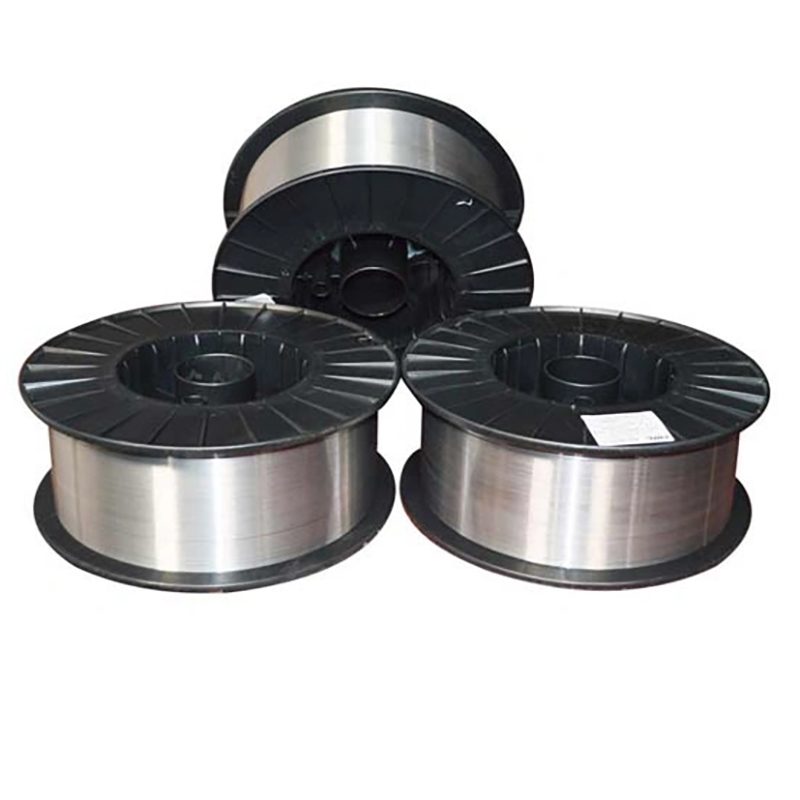
E71T-11
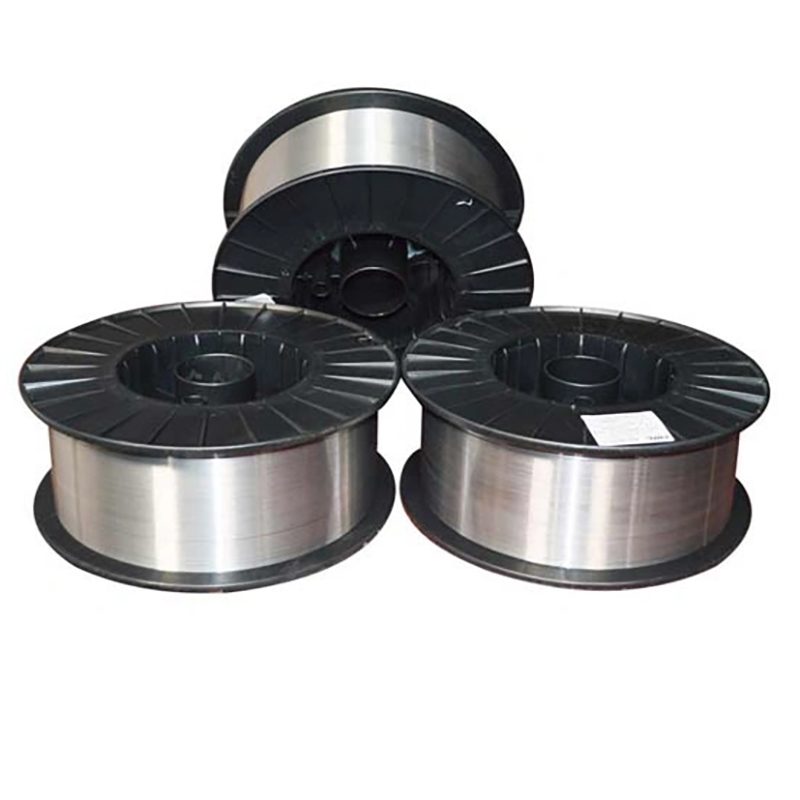
E71T-GS
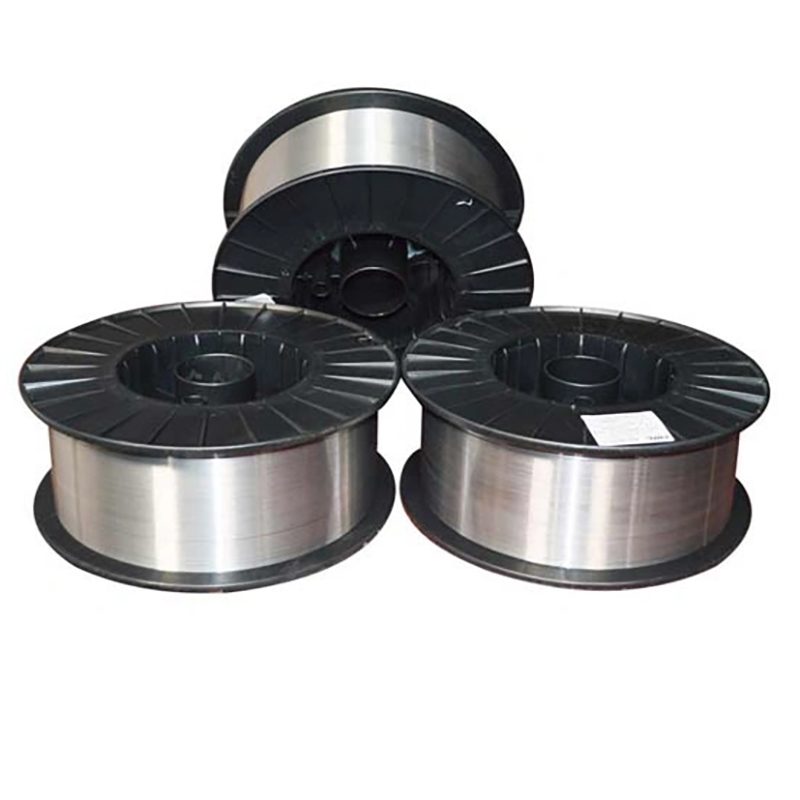
E81T1-B2C
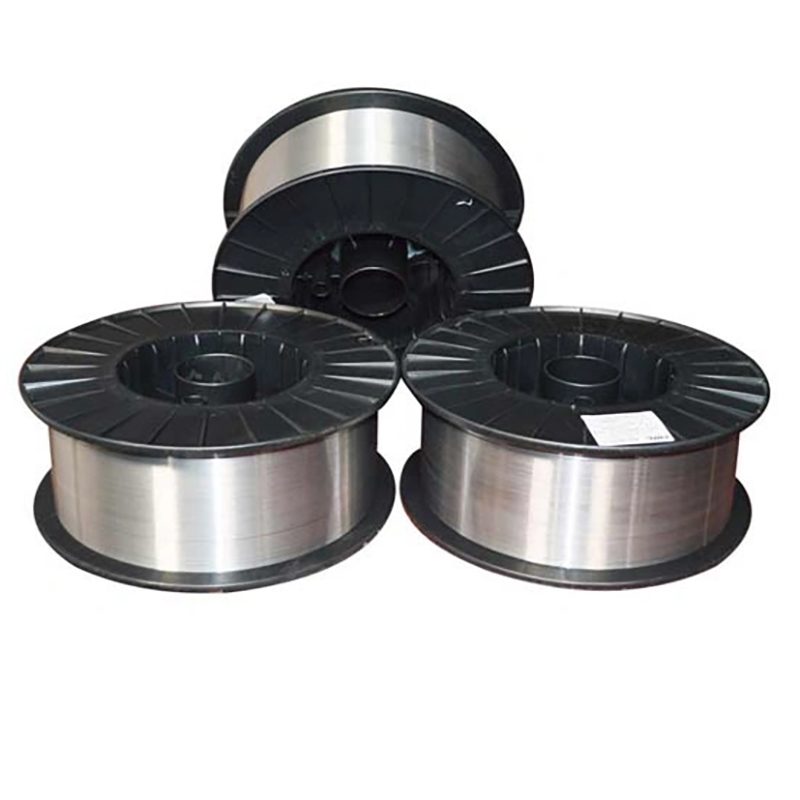
E91T1-B3C
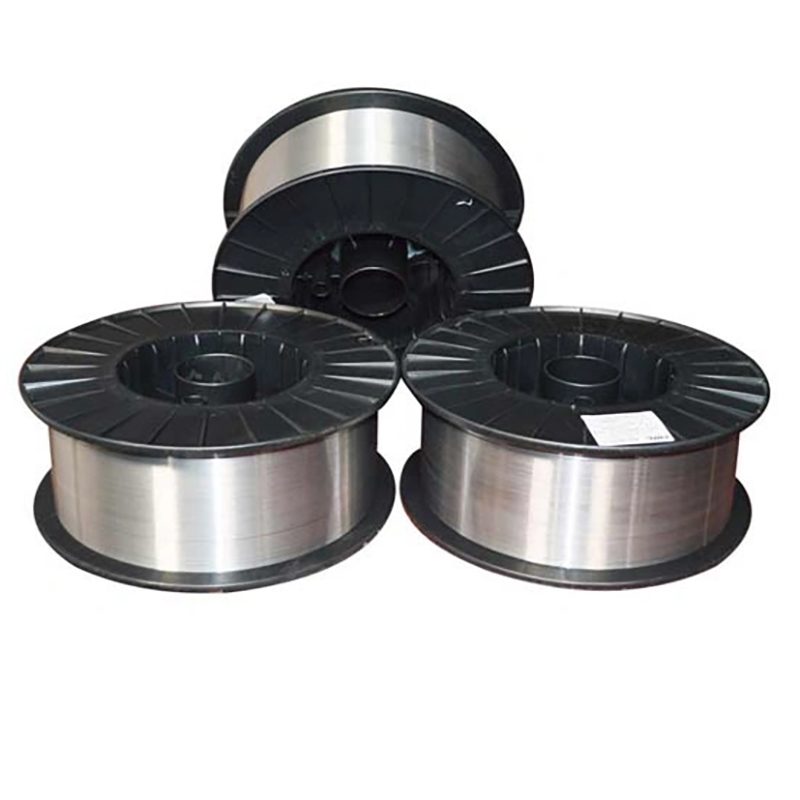
E81T1-Ni1C
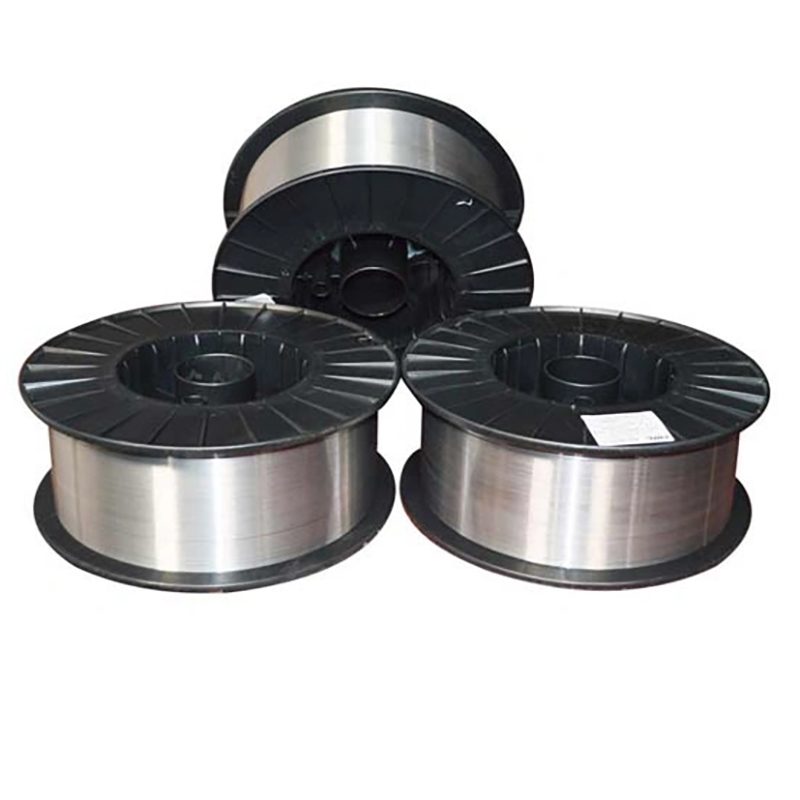
E81T1-Ni2C
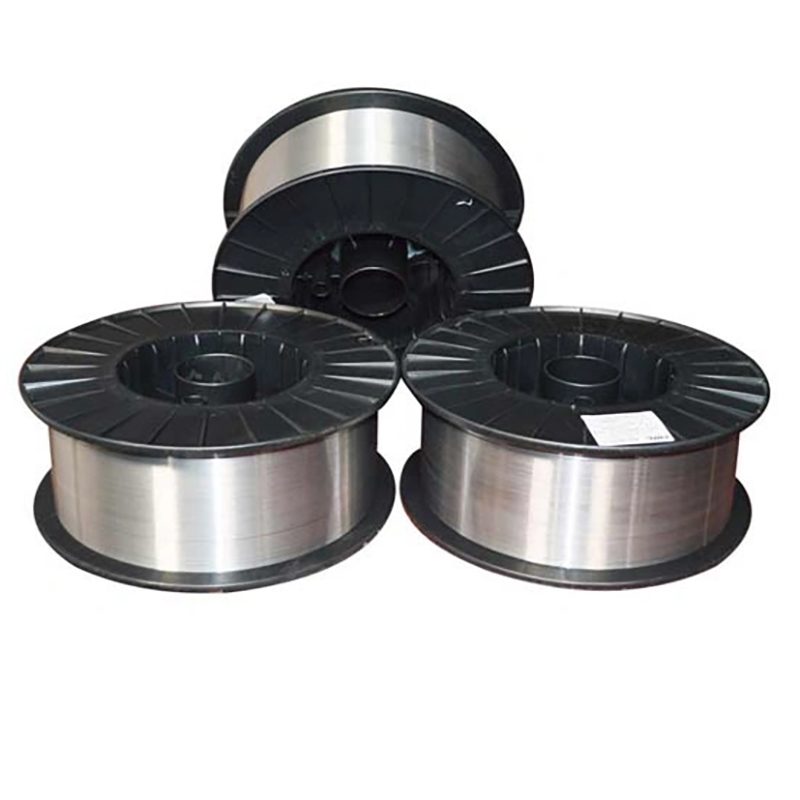
E81T1-K2C
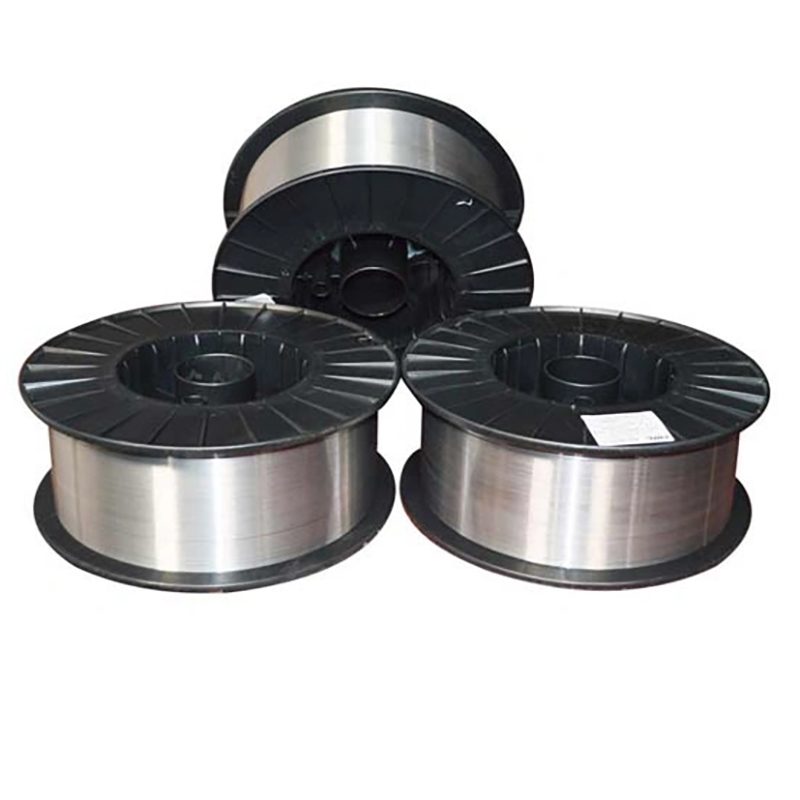
E81T1-W2C
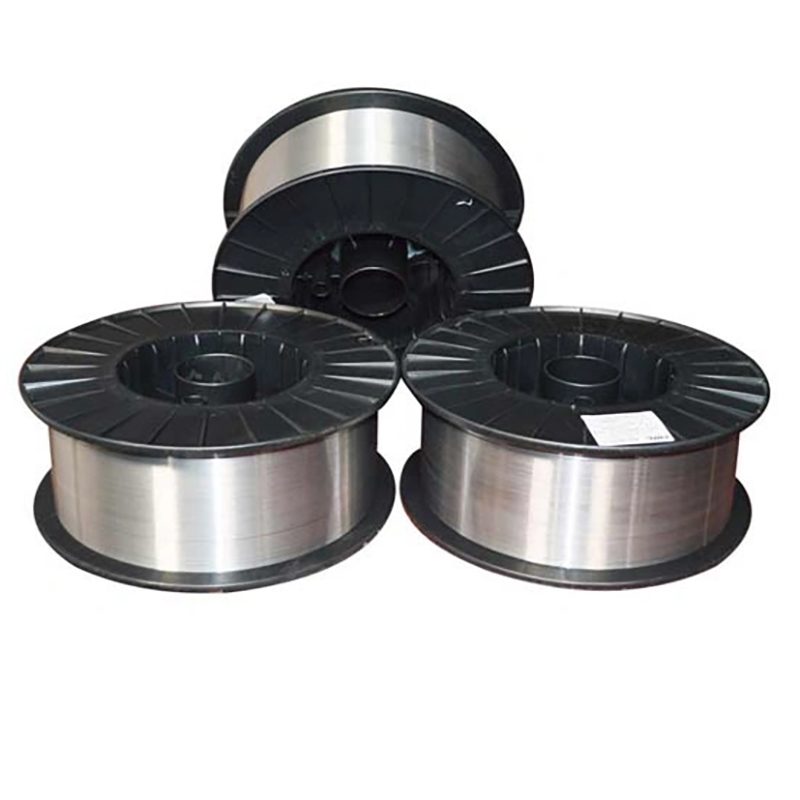
E308LT1-1
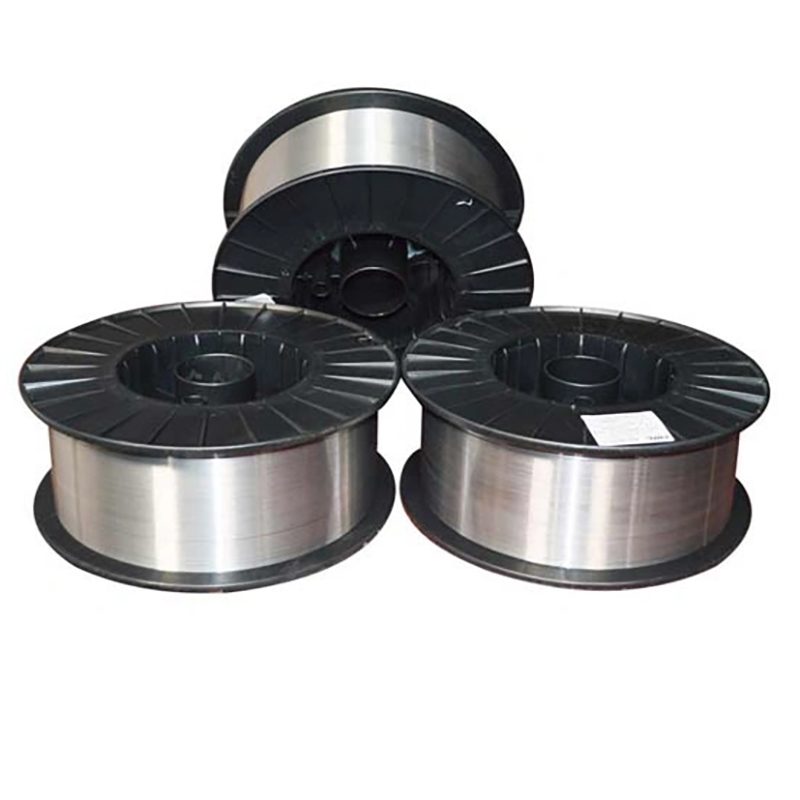
E309LT1-1

All You Need To Know About Flux Cored Welding Wire
Flux Cored Welding Wire is a unique type of welding consumable that contains a flux material within the core of the wire. This flux material eliminates the need for an external shielding gas, making this wire versatile for both manual and automated welding processes. For various industrial applications, Flux Cored Welding Wire is chosen for its exceptional weld quality and efficiency.
Because Flux Cored Welding Wire offers robust mechanical properties and is cost-effective, it is widely used in industries requiring welding operations. The ease of use and minimal maintenance make it a preferred choice for many professionals. Flux Cored Welding Wire can be utilized in different welding processes, including Gas Metal Arc Welding (GMAW) and Flux Cored Arc Welding (FCAW), adapting to various welding needs.
This article equips you with everything you need to know about Flux Cored Welding Wire. You’ll discover its applications, composition, the underlying mechanism of how it functions, and the various types of Flux Cored Welding Wire available. Towards the end, you can explore the distinctions between Flux Cored Welding Wire and other welding wires, helping you make an informed decision for your specific requirements.
How Does Flux Cored Welding Wire Work?
Flux Cored Welding Wire contains a flux material in its core, eliminating the need for external shielding gas. During welding, the wire is fed into the weld pool, and an electric arc melts the wire. As the wire melts, the flux reacts with the weld pool, creating a shielding gas that protects the weld from contamination. The continuous feeding of the wire and the reaction of the flux provide ongoing protection, making Flux Cored Welding Wire a flexible and efficient choice for various applications.
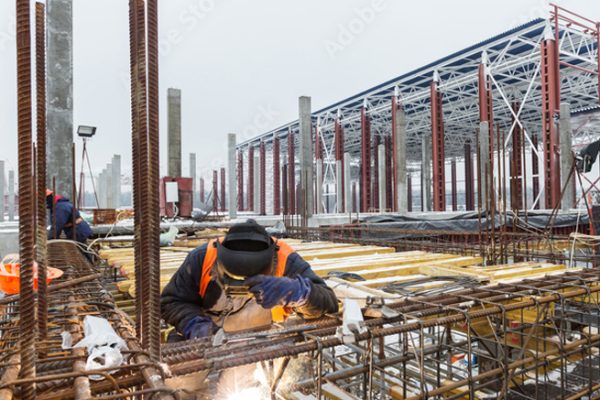
What Are Flux Cored Welding Wires Used For?
Flux Cored Welding Wires are versatile and find applications in various industries that require robust welding solutions. These could be the following:
- Automotive Manufacturing
- Shipbuilding Industry
- Construction Industry
- Aerospace Industry
- Pipeline Fabrication
- Heavy Equipment Manufacturing
- Railroad Construction
- Oil and Gas Industry
- Power Generation
- Metal Fabrication
Considerations When Buying Flux Cored Welding Wire
A Comprehensive Guide to Making the Right Choice
01.
ype of Welding Process:
- MIG (Metal Inert Gas) Welding: Flux Cored Welding Wire is often used in MIG welding, where it provides a smooth and stable arc, excellent weld appearance, and minimal spatter.
- FCAW (Flux-Cored Arc Welding): Specifically designed for this process, Flux Cored Welding Wire offers high deposition rates and deep penetration.
02.
Material Compatibility
- Carbon Steel: Ensure that the Flux Cored Welding Wire is compatible with the carbon steel you are welding.
- Stainless Steel & Other Alloys: Some Flux Cored Welding Wires are designed for welding specific alloys, so choose accordingly.
03.
Wire Diameter & Packaging
- Diameter: Available in various diameters, typically ranging from 0.8mm to 2.4mm. Select based on the thickness of the material being welded.
- Packaging: Consider spool sizes and packaging that suit your production volume and storage capabilities.
04.
Quality & Certification
- Quality Assurance: Look for Flux Cored Welding Wire that meets international quality standards.
- Certification: Ensure that the product has the necessary certifications, such as AWS, ISO, or other relevant industry standards.
When purchasing Flux Cored Welding Wire, it’s essential to consider the welding process, material compatibility, wire diameter, packaging, quality, and certification. Understanding these factors will guide you in selecting the right product that meets your specific needs and industry standards. For more detailed information and personalized recommendations, don’t hesitate to contact our experts.
Safety and Handling Instructions for Flux Cored Welding Wire
Ensuring Optimal Performance and Safety in Welding Operations
Proper Welding Technique
- Understanding the Process: Flux Cored Welding Wire is used in FCAW, which requires specific techniques and settings. Proper training and understanding of the process are essential.
- Arc Control: Maintain a steady and appropriate travel speed to prevent issues like slag inclusions and incomplete fusion.
Selection of Appropriate Shielding Gas
- Gas Type: Depending on the specific application and material, select the appropriate shielding gas to ensure optimal weld quality.
- Flow Rate: Adjust the flow rate of the shielding gas according to the manufacturer’s recommendations.
Wire Diameter and Type Consideration
- Compatibility: Select the correct wire diameter and type based on the material being welded and the welding process used.
- Consult Manufacturer Guidelines: Refer to the manufacturer’s guidelines for specific recommendations.
Correct Storage and Handling
- Storage Conditions: Store the wire in a clean, dry area to prevent moisture absorption, which can lead to poor weld quality.
- Handling Precautions: Handle with care to avoid damaging the wire’s surface, which could affect its performance.
Safety Equipment and Ventilation
- Personal Protective Equipment (PPE): Always use appropriate safety gear, including welding helmets, gloves, and protective clothing.
- Ventilation: Ensure proper ventilation in the work area to prevent the accumulation of potentially harmful fumes.
Regular Maintenance and Inspection
- Equipment Maintenance: Regularly inspect and maintain the welding equipment to ensure optimal performance and safety.
- Wire Inspection: Check the Flux Cored Welding Wire for any signs of damage or contamination before use.
Technical Specifications of Flux Cored Welding Wire for MIG and TIG Welding
Comprehensive Details for Professional Welding Applications
Flux Cored Welding Wire is a vital component in modern welding applications, particularly in MIG (Metal Inert Gas) and TIG (Tungsten Inert Gas) welding. Below, you will find a table summarizing the key technical specifications that professionals often consider when selecting Flux Cored Welding Wire:
Specification | Description |
---|---|
Wire Type | Self-Shielded / Gas-Shielded |
Alloy Composition | Various alloys including mild steel, stainless steel, and nickel alloys |
Diameter Range | Commonly ranges from 0.030″ to 1/8″ |
Tensile Strength | Varies based on alloy, typically in the range of 70,000 to 110,000 psi |
Current Type | DC+ (Electrode Positive) or DC- (Electrode Negative) |
Shielding Gas Requirements | For Gas-Shielded type: Commonly CO2 or CO2/Ar mix; Self-Shielded type: None required |
Welding Positions | Suitable for all positions (F, H, V, OH) |
Applications | Automotive, Shipbuilding, Construction, Aerospace, Pipeline Fabrication, etc. |
Flux Cored Welding Wire offers flexibility and efficiency in various welding processes. Understanding the technical specifications is essential for selecting the right wire for your specific application. For more detailed information or assistance in choosing the right Flux Cored Welding Wire for your needs, please don’t hesitate to contact us. Our team of experts is here to provide you with the professional guidance and support you require.
Safety and Handling Instructions for Flux Cored Welding Wire
Using Flux Cored Welding Wire safely and effectively requires understanding and following certain guideline
01.
Proper Welding Technique
Utilize a drag technique while welding with Flux Cored Welding Wire. Keep a consistent and suitable travel speed to avoid the weld pool from overtaking the arc, which might cause slag inclusions.
02.
Correct Wire Selection
Choose the right diameter and type of Flux Cored Welding Wire for your specific application. The wrong selection can lead to issues such as spatter and poor weld appearance.
03.
Storage of Welding Wire
Store Flux Cored Welding Wire in a clean, dry area. Moisture or contaminants can harm the wires, leading to subpar weld quality. If the wire is in use, remove the spool from the feeder and store it in a sealed container to minimize moisture exposure.
04.
Temperature Considerations
Keep a consistent temperature in both the storage area and the welding environment. Moving wires from a cold storage to a warm welding area can cause condensation, leading to rust and potential feeding issues.
05.
Safety Equipment
Always employ proper safety equipment, including helmets, gloves, and flame-resistant clothing. Make sure the workspace is well-ventilated to avoid the buildup of harmful fumes.
06.
Training and Certification
Familiarize yourself with Flux Cored Welding Wire through proper training and certification if you’re new to this type of welding. Mastery of the process ensures quality and efficiency in your welding tasks.
Remember, safety and adherence to best practices are paramount when working with Flux Cored Welding Wire. Always follow the manufacturer’s guidelines and industry standards to guarantee a safe and productive work environment.
Request Your Free WOERDE Welding Wire Sample
Experience WOERDE’s superior welding wires firsthand. Fill out our online form to request a free sample today. Discover why global businesses trust WOERDE.