
EM13K -Submerged Arc Welding Wire
Used together with fused flux SJ301 or sintered flux SJ101.Used for both high speed welding and filling welding on 50kg class base metals.Mostly used for welding boilers, pressure vessels,bridges,ships,etc.
What is EM13K
It is a kind of welding wire with appropriate manganese and silicon content.It matches with low-manganese and low-silicon type welding flux.It is not sensitive to the rust on the base metal.It has excellent bead molding,excellent slag detachability and high welding efficiency.
The structure of submerged arc welding (SAW) wire consists of several components that work together to facilitate the welding process. Here are the main constituents of submerged arc welding wire:
Core Wire:
The core wire is the primary component of the welding wire. It is typically made of a specific alloy or combination of alloys that are suitable for the intended welding application. The core wire serves as the electrode and provides the filler metal for the weld.
Flux:
Submerged arc welding involves the use of a granular flux, which is a mixture of various compounds. The flux serves multiple purposes in the welding process:
It creates a protective shield over the welding arc, preventing atmospheric contamination of the weld pool.
It provides deoxidizing and alloying elements to improve the quality of the weld.
It influences the characteristics of the weld bead and the cooling rate of the molten metal.
Coating:
The core wire is often coated with a thin layer that helps protect it during storage and transportation. This coating may contain anticorrosive substances to prevent rusting and ensure the wire’s integrity.
Surface Treatment:
Some submerged arc welding wires undergo specific surface treatments to enhance their performance. This could include processes such as copper coating to improve electrical conductivity or promote better arc stability.
Alloying Elements (if applicable):
Depending on the specific requirements of the welding application, additional alloying elements may be included in the core wire to achieve desired mechanical and metallurgical properties in the welded joint.
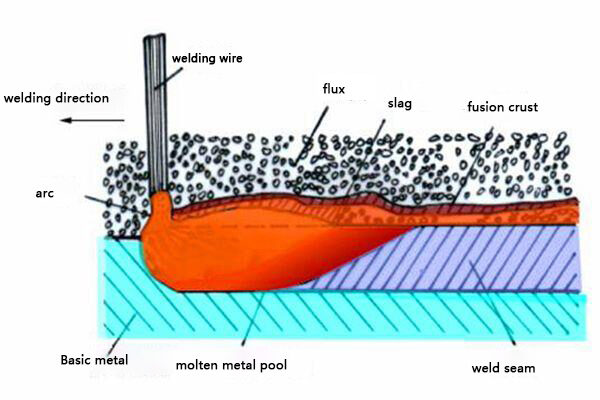
Typical Chemical Composition of welding wire(%) |
||||||
C |
Mn |
Si |
P |
S |
Cu |
other |
0.089 |
1.01 |
0.61 |
0.016 |
0.016 |
0.110 |
Typical Mec |
hanical Properti |
es of The Deposited Metal(Using with SJ301 |
||
Yield Strength ReL/Rpo.2 (Mpa |
Tensile Strength Rm(Mpa) |
Elongation δs(%) |
mpact test |
|
Temperature (℃) |
Impact Energy KV2(J) |
|||
425 |
535 |
32 |
-20℃ |
110 |
Packing terms |
|||||
Diameter |
2.0mm |
2.4mm |
3.2mm |
4.0mm |
4.8mm |
Small coil (Inner Dia 300mm)25kg |
√ |
√ |
√ |
√ |
√ |
Large coil (Inner Dia 550mm,630mm) 100kg,150kg,200kg,250kg,350kg |
√ |
√ |
√ |
√ |
√ |
Metal spool (Inner Dia 300mm)25kg |
√ |
√ |
√ |
√ |
√ |
Submerged arc welding (SAW) wire is utilized in various industries due to its suitability for welding thick materials and its high deposition rates. Some of the key industries where submerged arc welding wire finds applications include:
Shipbuilding:
Submerged arc welding is commonly used in shipbuilding for welding large and thick steel plates, structures, and components.
Construction:
The construction industry employs submerged arc welding for welding structural steel components used in buildings, bridges, and other infrastructure projects.
Oil and Gas:
Submerged arc welding is used in the fabrication of pipelines, storage tanks, and other equipment in the oil and gas industry.
Railroad:
The railroad industry utilizes submerged arc welding for the fabrication and repair of rail tracks and components.
Heavy Equipment Manufacturing:
Manufacturers of heavy machinery and equipment, such as mining machinery and construction equipment, often use submerged arc welding for its efficiency in welding thick materials.
Automotive:
While not as common as other welding processes in the automotive industry, submerged arc welding is employed for specific applications, such as welding large vehicle components.
Aerospace:
Submerged arc welding may be used in the aerospace industry for specific applications where its characteristics are advantageous.
Power Generation:
Submerged arc welding is used in the fabrication of power generation equipment, including components for thermal and nuclear power plants.
Pressure Vessel Manufacturing:
Industries involved in the fabrication of pressure vessels, such as those used in chemical processing, may utilize submerged arc welding for its ability to produce high-quality welds in thick materials.
Mining:
Submerged arc welding is employed in the mining industry for welding components of heavy-duty mining equipment.
Bridge Construction:
Submerged arc welding is commonly used in the construction and repair of bridges, where thick steel plates and structures are prevalent.
Wind Energy:
Submerged arc welding is used in the fabrication of components for wind turbines and their support structures.
Nuclear Industry:
In the nuclear industry, submerged arc welding may be employed for certain applications due to its ability to produce sound welds in thick materials.
General Manufacturing:
Submerged arc welding is used in various manufacturing industries where thick steel components need to be joined efficiently.
AWS A5.X – Specification for Filler Metals:
- The American Welding Society (AWS) A5.X series includes various specifications for filler metals. For SAW wire, the applicable standard would depend on the type of material used. For example, AWS A5.17 covers carbon steel electrodes and fluxes for SAW.
ISO 14171 – Welding consumables – Solid wire electrodes, tubular cored electrodes, and electrode/flux combinations for submerged arc welding of non-alloy and fine-grain steels – Classification:
- This International Organization for Standardization (ISO) standard provides classification requirements for solid wire electrodes used in SAW of non-alloy and fine-grain steels.
AWS QC1 – Standard for AWS Certification of Welding Inspectors:
- Compliance with AWS QC1 ensures that welding inspectors involved in the production process are certified and qualified to maintain quality control.
ISO 3834 – Quality requirements for fusion welding of metallic materials:
- This ISO standard specifies quality requirements for welding processes, ensuring that the manufacturing process adheres to quality control measures.
ISO 9001 – Quality Management Systems:
- Adherence to ISO 9001 ensures the implementation of a comprehensive quality management system, covering various aspects of production, testing, and quality control.
ISO 14001 – Environmental Management Systems:
- Compliance with ISO 14001 ensures that environmental management standards are followed during the production process, addressing issues such as waste management and resource efficiency.
AWS A5.23/A5.23M – Specification for Low-Alloy Steel Electrodes and Fluxes for Submerged Arc Welding:
- This AWS standard provides specific requirements for low-alloy steel electrodes and fluxes used in SAW applications.
AWS A5.28/A5.28M – Specification for Low-Alloy Steel Filler Metals for Gas Shielded Arc Welding:
- If the SAW wire is designed for gas-shielded arc welding applications, compliance with this AWS standard may be relevant.
Customer Specifications:
- Manufacturers should also consider any customer-specific specifications or requirements that may be applicable to the production of SAW wire.
Request Your Free WOERDE Welding Wire Sample
Experience WOERDE’s superior welding wires firsthand. Fill out our online form to request a free sample today. Discover why global businesses trust WOERDE.