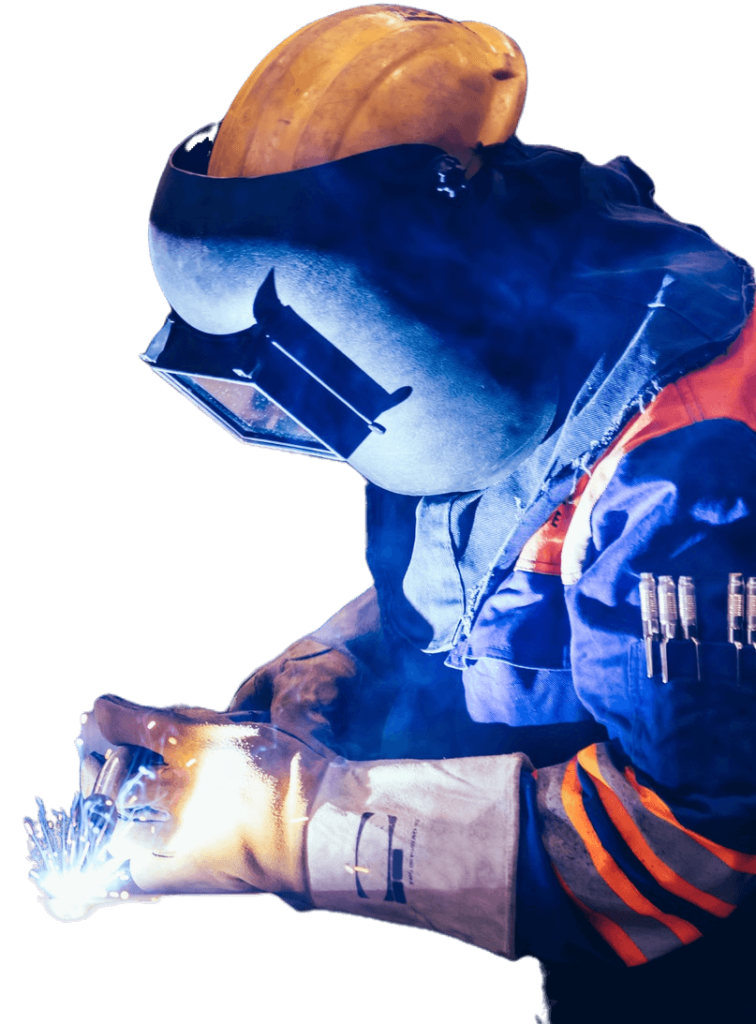
ALUMINUM ALLOY WELDING WIRE
WOERDE is a renowned industrial welding consumables manufacturer that offers an extensive range of welding wires. Our state-of-the-art manufacturing facility in China produces high-quality Aluminum Alloy Welding Wire, designed to meet the rigorous demands of various industrial applications.
WOERDE’s product line includes a diverse array of welding wires, such as solid copper, flux-cored, stainless steel, aluminum, and copper welding wires, along with electrodes. Our Aluminum Alloy Welding Wire is particularly favored in industries like automotive, aerospace, and shipbuilding, where its unique properties are essential.
Aluminum Alloy Welding Wire belongs to the family of arc welding consumables and is known for its lightweight yet robust nature. It’s often used with Gas Metal Arc Welding (GMAW) or Tungsten Inert Gas (TIG) welding processes, where a shielding gas protects the weld pool from atmospheric contamination. The advantages of WOERDE’s Aluminum Alloy Welding Wire include its excellent conductivity, corrosion resistance, and enhanced weldability, making it reliable, easy to use, and requiring less maintenance.
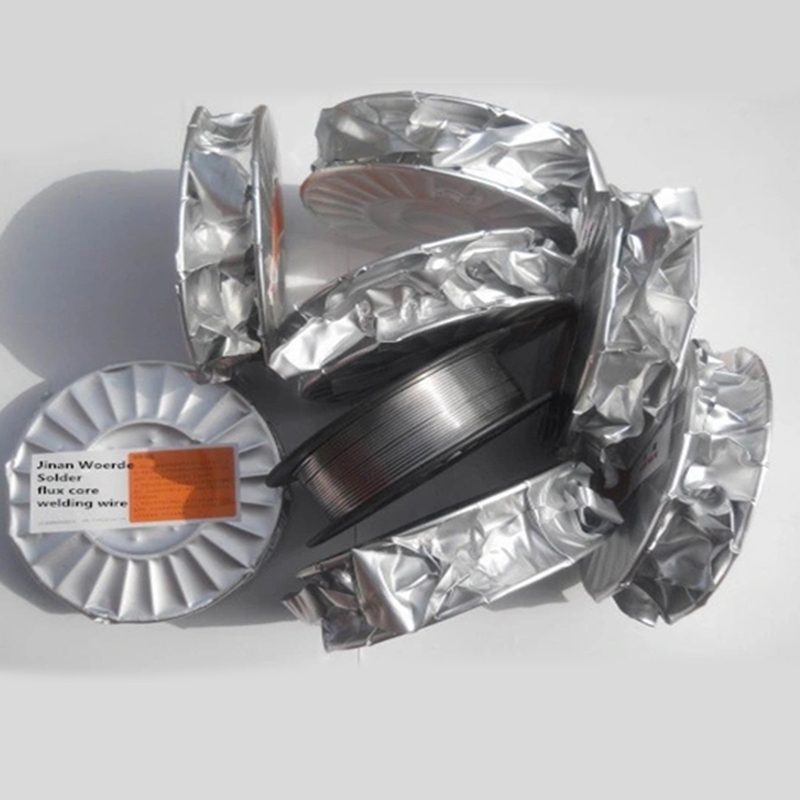
All You Need To Know About Aluminum Alloy Welding Wire
Aluminum Alloy Welding Wire is a specialized welding consumable designed for joining aluminum and its alloys. Suitable for both manual and automated processes, it’s widely used in industries like automotive, aerospace, and construction for its exceptional weld quality, strength, and efficiency. The wire’s compatibility with various welding methods, such as Gas Metal Arc Welding (GMAW), Tungsten Inert Gas (TIG) Welding, and Metal Inert Gas (MIG) Welding, adds to its versatility.
Known for its excellent mechanical properties, including high tensile strength and corrosion resistance, Aluminum Alloy Welding Wire is a cost-effective solution that requires minimal maintenance. It can be used with different shielding gases like pure argon or argon-helium mixtures, ensuring protection against atmospheric contamination.
This article provides an overview of Aluminum Alloy Welding Wire, covering its specific applications, unique characteristics, and the underlying principles of how it functions. Whether you’re a professional in the field or someone interested in learning more about this essential welding material, understanding Aluminum Alloy Welding Wire’s role in modern manufacturing and fabrication is key to appreciating its value in today’s industrial landscape.
How Does Aluminum Alloy Welding Wire Work?
Aluminum Alloy Welding Wire is a vital component in welding aluminum materials, acting as a filler metal. During the welding process, the wire is fed through a welding gun into the weld pool, aligning parallel to the workpiece. An electric arc is then established between the wire and the workpiece, initiating the welding operation.
The diameter of Aluminum Alloy Welding Wire is typically selected to be smaller than the thickness of the materials being welded. As the welding begins, the wire melts, fusing with the base aluminum metal to create a strong and durable weld. Simultaneously, a shielding gas, often pure argon or an argon-helium mixture, is released from the welding gun. This gas protects the weld pool from atmospheric contamination, ensuring a clean and defect-free weld.
The process continues with the wire being steadily fed and the shielding gas consistently released, maintaining the integrity of the weld. The unique properties of Aluminum Alloy Welding Wire, such as its compatibility with aluminum’s thermal conductivity and oxide layer, make it an essential choice for welding operations involving aluminum and its alloys.
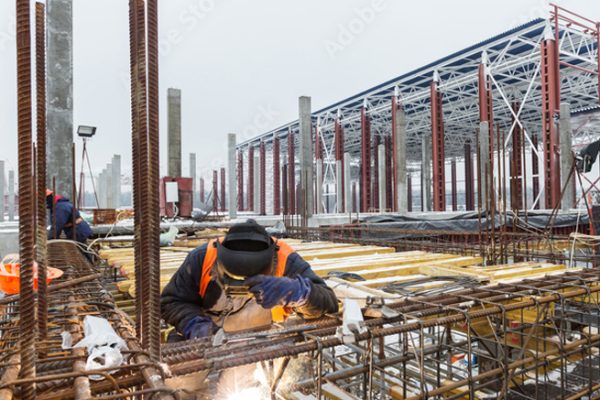
What Are Aluminum Alloy Welding Wires Used For?
Aluminum Alloy Welding Wires are utilized across various industries that require specialized welding operations for aluminum materials. These include
- Automotive Manufacturing
- Aerospace Industry
- Shipbuilding Industry
- Construction Industry
- Electrical Industry
- Railroad Construction
- Bicycle Manufacturing
- Food and Beverage Packaging
- Power Generation
- Metal Fabrication
Considerations When Buying Aluminum Alloy Welding Wire
A Comprehensive Guide to Selecting the Right Welding Wire for Your Needs
01.
Material Compatibility
- Alloy Match: Ensure that the Aluminum Alloy Welding Wire is compatible with the specific aluminum alloy you are welding. Different aluminum alloys require specific filler materials to achieve optimal weld quality.
- Corrosion Resistance: Consider the environmental conditions where the weld will be exposed. Select a wire that offers the required corrosion resistance.
02.
Welding Process Requirements
- Welding Technique: Determine the welding process you will be using, such as MIG or TIG, and choose the wire accordingly.
- Shielding Gas: Aluminum Alloy Welding often requires specific shielding gases. Ensure that the wire you select is suitable for the gas you plan to use.
03.
Quality and Manufacturer Reputation
- Certifications: Look for wires that meet industry standards and certifications, ensuring quality and consistency.
- Brand Reputation: Choose a reputable manufacturer known for producing high-quality aluminum alloy welding wires.
04.
Application Specifics
- Thickness of Materials: The wire diameter should match the thickness of the materials being welded. Consult with the manufacturer’s guidelines or a welding professional to select the appropriate wire size.
- Desired Mechanical Properties: Consider the required mechanical properties of the weld, such as tensile strength and ductility. Select a wire that can achieve these properties in the specific application.
Selecting the right Aluminum Alloy Welding Wire is a critical step in achieving successful welding results. By considering material compatibility, welding process requirements, quality standards, and specific application needs, you can make an informed decision that aligns with your project’s demands.
Benefits of Using Aluminum Alloy Welding Wire
A Comprehensive Guide to Selecting the Right Welding Wire for Your Needs
Material Compatibility
- Smooth Welding Experience: Aluminum Alloy Welding Wire offers a smooth and stable arc, reducing spatter and ensuring clean welds.
- High Strength: The specific alloying elements in the wire provide excellent tensile strength, making it suitable for demanding applications.
Enhanced Corrosion Resistance:
Long-lasting Welds: Aluminum Alloy Welding Wire provides welds that resist corrosion, especially in harsh environmental conditions, ensuring durability.
Ease of Use
- User-Friendly: Aluminum Alloy Welding Wire is known for its ease of use, making it suitable for both professionals and hobbyists.
- Reduced Cleaning Time: The wire’s quality ensures minimal post-weld cleanup, saving time and effort.
Versatility in Applications
- Wide Industry Usage: From automotive to aerospace, construction, and marine applications, Aluminum Alloy Welding Wire is versatile and meets various industry requirements.
- Compatibility with Different Processes: Suitable for both MIG and TIG welding processes, offering flexibility in welding techniques.
Cost-Effectiveness
- Efficient Welding: The wire’s consistent diameter and quality contribute to efficient welding, reducing waste and saving costs.
- Availability in Various Sizes: Available in different diameters and packaging options, allowing for customization based on project needs.
Environmental Considerations
- Recyclable Material: Aluminum is a recyclable material, making Aluminum Alloy Welding Wire an environmentally friendly option.
- Energy Efficient Manufacturing: Many manufacturers focus on energy-efficient production processes, contributing to sustainability.
Technical Specifications of Aluminum Alloy Welding Wire for MIG and TIG Welding
Detailed Information for Welding Professionals
Specification | MIG Welding | TIG Welding |
---|---|---|
Wire Diameter (mm) | 0.8, 1.0, 1.2, 1.6 | 1.0, 1.6, 2.4, 3.2 |
Weight (kg) | Spools: 7kg, 15kg | Straight Lengths: 5kg, 10kg boxes |
Alloy Type | ER4043, ER5356, ER4047, etc. | ER4043, ER5356, ER4047, etc. |
Tensile Strength (MPa) | 275-310 (depending on alloy) | 275-310 (depending on alloy) |
Yield Strength (MPa) | 125-165 (depending on alloy) | 125-165 (depending on alloy) |
Elongation (%) | 8-15% (depending on alloy) | 8-15% (depending on alloy) |
Shielding Gas | Argon 100%, or Argon-Helium 75%/25% | Argon 100% |
Melting Temperature (°C) | 575-635 (depending on alloy) | 575-635 (depending on alloy) |
Applications | Automotive, Aerospace, Shipbuilding, Construction | Precision Welding in Aerospace, Automotive, etc. |
For more detailed and specialized information tailored to your specific needs, please don’t hesitate to contact us. Our team of experts is ready to provide you with personalized assistance and send you professional materials that align with your welding projects. Reach out to us today, and let’s build something extraordinary together!
Safety and Handling Instructions for Aluminum Alloy Welding Wire
Enhancing Welding Efficiency with Precision and Care
01.
Welding Process and Techniques
- GMAW Method: Utilizing electric arc forms between a consumable MIG wire electrode and workpiece metals.
- Metal Transfer Modes: Globular, short-circuiting, and spray, each with distinct properties and advantages.
- Versatility: Suitable for welding aluminum, steel, and other non-ferrous materials.
02.
Equipment and Components
- Welding Gun: Comprises control switch, contact tip, power cable, gas nozzle, and gas hose.
- Power Supply: Constant voltage power supply commonly used; direct current employed with positively charged electrode.
- Shielding Gas: Selection based on material being welded; mixtures of argon, carbon dioxide, oxygen, helium, etc.
03.
Quality and Performance
- Dross and Porosity Control: Ensuring clean electrodes and workpieces, proper welding speed, and current settings.
- High Deposition Rate: Allows welding speeds of up to 110 mm/s (250 in/min).
04.
Safety Measures
- Protective Clothing: Includes heavy gloves and protective long sleeve jackets.
- Eye Protection: Helmets with dark face plates or liquid crystal-type face plates that self-darken upon exposure to the arc.
05.
Application and Industry Usage
- Industrial Environments: Preferred for its speed, versatility, and adaptability to robotic automation.
- Automobile Industry: Often used for arc spot welding, replacing riveting or resistance spot welding.
06.
Environmental Considerations
- Outdoor Usage: Rarely used outdoors or in areas of moving air due to shielding gas requirements.
- Hazardous Gases: Proper ventilation required to avoid exposure to hazardous gases and airborne particulate matter.
Our Aluminum Alloy Welding Wire is designed to meet the diverse needs of modern welding applications. With its superior quality, safety features, and adaptability to various welding methods, it stands as a reliable choice for professionals and industries alike.
Request Your Free WOERDE Welding Wire Sample
Experience WOERDE’s superior welding wires firsthand. Fill out our online form to request a free sample today. Discover why global businesses trust WOERDE.